Maintaining Methods of Dry Air Generator for Transformer
Dry Air generators are widely used in the electric industry, where large equipment such as transformers and reactors require dry air during maintenance. The dry air provided can ensure that the internal insulation of power equipment will not be damp, and maintenance personnel will not suffocate due to lack of oxygen when working inside the equipment. It is safer, more reliable, economical, and convenient than using bottled gas. However, just like any other equipment, dry air generators require proper and consistent maintenance to ensure optimal performance and longevity. This article delves into the essential components of these generators, outlines key maintenance procedures, addresses common troubleshooting issues, and emphasizes the importance of preventative care.
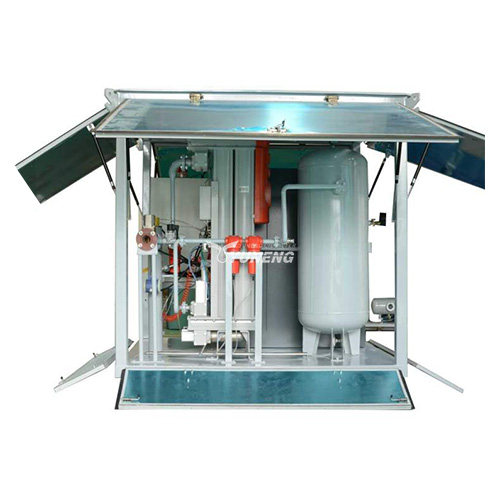
Essential Components of Dry Air Generator
Understanding the essential components that make up a dry air generator is the first step towards effective maintenance.
1. The Engine of the System: Air Compressor
The air compressor serves as the engine of the dry air generator, setting the airflow in motion. Its primary function is to compress the ambient air, increasing its pressure to initiate the drying process. The selection of the compressor, whether oil-injected or oil-free, hinges on the specific requirements of the transformer and the desired output of the dry air generator. Capacity is also a crucial factor, as it determines the volume of air the compressor can handle.
2. Combating Bulk Moisture: Refrigerated Air Drying System
As the compressed air exits the compressor, it carries a significant amount of moisture. The refrigerated air drying system steps in to tackle this challenge. It acts as a moisture separator, efficiently removing bulk moisture in the form of condensation. This system typically employs a heat exchanger, which functions like a radiator in your car. By cooling the compressed air, the water vapor condenses and separates from the air stream, leaving behind drier air.
3. Achieving Ultra-Low Moisture Levels: Adsorption Drying System
While the refrigerated air drying system tackles the majority of the moisture, it might not be enough for applications requiring exceptionally dry air, such as protecting transformers. This is where the adsorption drying system takes center stage. It employs desiccants, specialized materials renowned for their moisture-absorbing prowess. These desiccants, often zeolites or alumina, have a high affinity for water vapor molecules, attracting and holding them on their surfaces.
Unlike the continuous operation of the previous systems, the adsorption drying system often utilizes two towers. This allows for an uninterrupted dry air supply. While one tower is actively drying the air, the other undergoes regeneration, a process that removes the captured moisture from the desiccant, ensuring its continued effectiveness.
4. Guardians of Purity: Filters
The dry air generator relies on filters to safeguard its internal components from harmful contaminants. These contaminants, in the form of dust, dirt, and other particulates, can damage delicate parts or compromise the quality of the dry air. Different types of filters are employed throughout the system, each serving a specific purpose:
- Pre-filters: These act as the first line of defense, capturing coarse particles like dust and debris.
- Coalescing filters: They specialize in removing liquid droplets that might form in the system.
- HEPA filters: These high-efficiency filters are particularly adept at capturing very fine particles, ensuring exceptionally clean and dry air reaches the transformer.
5. The Central Nervous System: Control System
The control system acts as the central nervous system of the dry air generator, meticulously monitoring and managing its operation. It comprises various sensors strategically placed throughout the system, keeping a watchful eye on:
- Pressure: Maintaining optimal pressure is crucial for efficient operation.
- Temperature: Monitoring temperature fluctuations helps identify potential issues.
- Dew point: Dew point, a measure of how much moisture the air can hold before condensation occurs, is a critical indicator of air dryness.
The control panel, the user interface of the system, allows for adjustments to various settings, enabling fine-tuning of the dry air generator’s performance. Additionally, it displays real-time data and alerts, empowering operators to proactively address any potential problems.
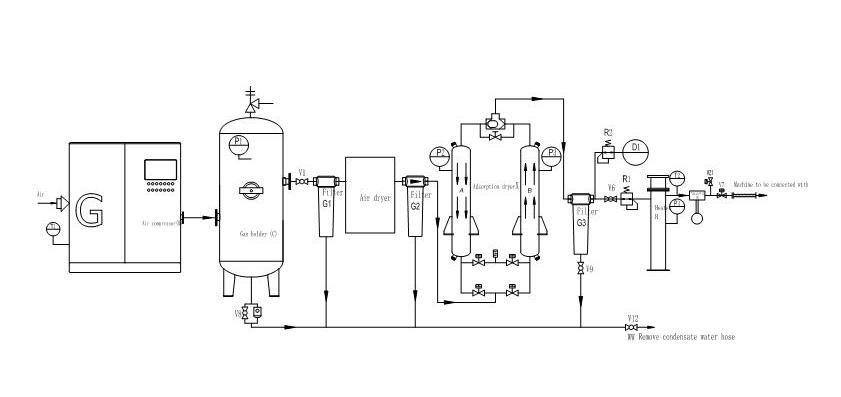
Key Maintenance Procedures for Dry Air Generator
Maintaining a dry air generator isn’t just about ensuring it functions; it’s about guaranteeing the continued health and protection of your valuable transformers. By adhering to specific maintenance procedures, you can proactively address potential issues, maximize the generator’s lifespan, and minimize the risk of transformer damage. Here are some key procedures to remember:
1. Proactive Inspections:
- Visual checks: Schedule regular inspections to visually examine the dry air generator for leaks, damaged components, or unusual wear and tear. Pay close attention to areas like connections, hoses, filters, and signs of corrosion or rust.
- Verifying readings: Regularly monitor and record pressure gauges and dew point monitors to ensure proper operation. Deviations from expected values, such as significantly lower pressure or higher dew point, may indicate potential problems like leaks, filter clogs, or desiccant saturation.
2. Filter Maintenance:
- Scheduled replacements: Follow the manufacturer’s recommendations for filter replacement intervals. In dusty environments, more frequent changes might be necessary to prevent them from becoming clogged and compromising airflow.
- Cleaning or disposal: Depending on the filter type, they might require cleaning or proper disposal after reaching their capacity. For example, pre-filters might be washable, while HEPA filters require replacement upon reaching their saturation point.
3. Desiccant Management:
- Regeneration/replacement: Adhere to the manufacturer’s guidelines for desiccant regeneration or replacement intervals. Regeneration, typically involving heat and purging, removes captured moisture from the desiccant, while replacement involves switching out the desiccant with a new one.
- Visual inspection: During regeneration or replacement, visually inspect the desiccant for signs of deterioration, such as cracking, discoloration, or caking. These signs signify the need for immediate replacement to maintain optimal moisture removal efficiency.
4. Oil and Lubricant Maintenance (if applicable):
- Oil changes and top-offs: If your dry air generator utilizes an oil-injected compressor, follow the manufacturer’s instructions for oil changes and top-offs to maintain optimal performance and lubrication. Using the manufacturer’s recommended oil ensures compatibility and avoids voiding warranties.
5. Calibration:
- Sensor and instrument calibration: Regularly calibrate sensors and instruments like pressure gauges and dew point monitors to ensure the accuracy of their readings. This helps ensure the system operates within the appropriate parameters and provides reliable data for monitoring purposes.
6. Operational Testing:
- Performance verification: Conduct periodic operational testing, simulating real-world scenarios, to verify the dry air generator’s performance under load. This proactive approach helps identify any potential issues before they escalate, preventing unexpected downtime and associated costs.
7. Additional Tips:
- Manufacturer’s guidance: Always consult the manufacturer’s manual for specific maintenance instructions and recommendations tailored to your dry air generator model.
- Seek professional help: Consider engaging qualified technicians for complex tasks, especially when dealing with critical components like desiccants or troubleshooting challenging issues beyond your expertise.
- Detailed maintenance log: Maintain a detailed maintenance logbook to record all maintenance activities, including dates, observations, actions taken, and replacement parts used. This logbook serves as a valuable resource for tracking the generator’s health, identifying trends over time, and providing valuable information for future maintenance activities or troubleshooting.
By incorporating these essential maintenance protocols and cultivating a proactive mindset, you can guarantee the consistent reliability of your dry air generator, thereby fortifying its role as a dependable guardian for your transformers. It is crucial to bear in mind that diligent and meticulously documented maintenance constitutes an investment with substantial long-term dividends, shielding you from expensive repairs and replacements while ensuring the seamless functionality of your transformers.
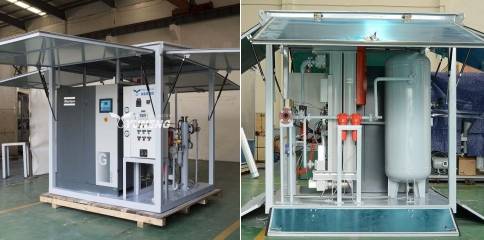
Troubleshooting Common Issues When Using Transformer Dry Air Machine
While Transformer Dry Air machines are robust systems, certain issues can occasionally arise. Here are some common problems and their potential solutions:
- Low dew point: This indicates insufficient drying and could be caused by clogged filters, malfunctioning refrigeration systems, or depleted desiccant material. Address the root cause by replacing filters, checking the refrigeration system, or regenerating/replacing desiccant.
- High pressure: This could be due to a malfunctioning pressure relief valve or clogged discharge line. Consult the manufacturer’s instructions for troubleshooting and repairs.
- Excessive noise or vibration: This could indicate loose components, worn bearings, or other mechanical issues. Contact a qualified technician for inspection and repairs.
- Important Note: If you encounter any issues beyond your expertise, always seek assistance from a qualified service technician for proper diagnosis and repair.
Important Note: If you encounter any issues beyond your expertise, always seek assistance from a qualified service technician for proper diagnosis and repair.
Importance of Preventative Maintenance for Dry Air Generator
Preventative maintenance for dry air generators is paramount for ensuring optimal performance and longevity. These machines play a critical role in safeguarding transformers by maintaining the insulation integrity through the removal of moisture, preventing potential damage, and extending their operational lifespan.
Regular maintenance procedures such as filter replacement, moisture level monitoring, and system checks not only enhance efficiency but also mitigate the risk of costly breakdowns or failures. By proactively addressing issues before they escalate, preventative maintenance reduces downtime, enhances reliability, and ultimately safeguards the integrity of the electrical system.
Moreover, consistent upkeep helps in identifying and rectifying minor faults or inefficiencies, thereby optimizing the performance of the dry air generator and ensuring an uninterrupted power supply. In essence, investing in preventative maintenance for dry air generators is an essential strategy to uphold the reliability, efficiency, and longevity of critical electrical infrastructure.
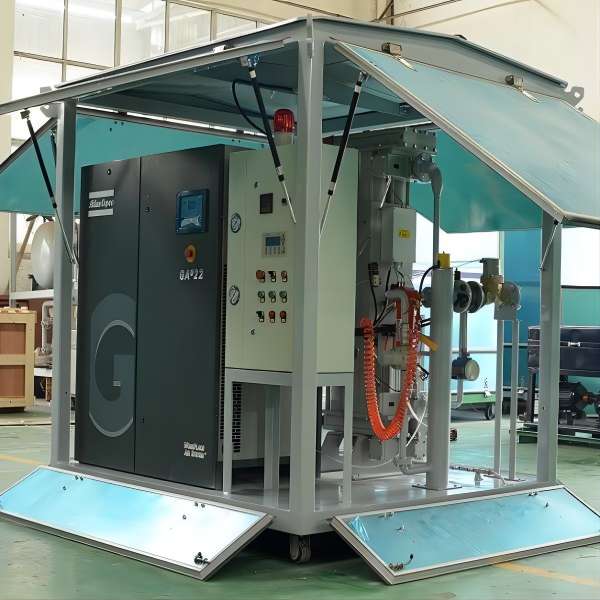
Get in Touch with China Oil Purifier: YUNENG
Chongqing YUNENG Oil Filter Manufacturing Co., Ltd. specializes in offering GF series transformer dry air generators, delivering comprehensive solutions for oil filtration needs. The GF Dry Air Generator exemplifies our mission to create innovative, reliable solutions for the power sector. This advanced technology, with its numerous benefits, ensures optimal transformer operation, prioritizes workforce safety, and guarantees the consistent energy supply that drives our world.
We are dedicated to meeting your requirements effectively. Don’t hesitate to contact us if you require our products or services.