ZJA Transformer Oil Filtration Machine: Optimizing Transformer Life and Efficiency
Maintaining optimal transformer oil conditions is paramount for ensuring the reliable and efficient operation of power equipment. To achieve this, dehydration, degassing, and oil filtration are crucial prerequisites before filling new transformers or performing maintenance on existing units. This document provides a comprehensive ZJA transformer oil filtration machine overview, highlighting its key components and functionalities.
Key Components of Transformer Oil Filtration Machine
1. Vacuum Dehydration and Degassing System
- Pump System: The system employs rotary vane vacuum pumps, with the option of integrating a booster pump for enhanced performance. This configuration facilitates the efficient removal of dissolved gases and moisture from the oil.
- Vacuum Chamber: The chamber houses a series of highly effective ring mesh elements that maximize the surface area exposed to the vacuum, optimizing the degassing and dehydration process.
- Vacuum Isolation Valves: Dedicated vacuum breaking valves are installed at both the inlet and outlet of the chamber, ensuring complete separation between the vacuum and pressure sides of the plant, preventing contamination and backflow.
2. Heating System
- Electrical Heaters: The system utilizes indirect heating via electrical elements with a surface efficiency below 1.1 W/cm². This controlled approach minimizes the risk of localized overheating and ensures uniform temperature distribution throughout the oil.
- Temperature Control: Precise temperature regulation is implemented to ensure optimal degassing and dehydration while preventing thermal degradation of the oil.
3. Filtration System
- Fine Filtration: At the outlet of the plant, the treated oil passes through a high-performance filter with a pore size of 0.5 microns or less. This effectively removes any remaining solid contaminants, ensuring the cleanliness and integrity of the oil.
- Filtration Media: The specific filtration media selection depends on the type and severity of the oil contamination. Options include depth filters, pleated filters, and cartridge filters.
4. Oil Transfer System
- Inlet Pump: The plant may be equipped with a positive displacement rotary inlet pump for efficient oil circulation and initial priming. This ensures smooth operation and minimizes downtime.
- Outlet Pump: A centrifugal closed-coupled high-suction pump is used at the outlet to deliver the treated oil back to the transformer or storage tank.
5. Controlling System
- Automation: The ZJA plant features a fully automatic control system, offering operator convenience and process consistency.
- PLC Logic: Programmable logic controllers (PLCs) are utilized for real-time monitoring and control of various plant parameters, including temperature, pressure, flow rate, and vacuum level.
- SCADA Interface (Optional): The system can be optionally integrated with a SCADA (Supervisory Control and Data Acquisition) system for remote monitoring, data logging, and centralized control.
6. Safety System
- Multiple Layers: The plant incorporates a comprehensive safety system to protect both the equipment and the operating personnel.
- Key Features: This system includes aeration valves to prevent air buildup, overheating protection mechanisms, and automatic level switches to detect potential leaks or overflows. Additionally, emergency shutdown protocols are in place to minimize risks and ensure safe operation.
7. Oil Flow Control System
- Automatic Regulation: The ZJA plant utilizes an automatic variable oil flow control system to optimize treatment efficiency and user experience during operation. This system adjusts the flow rate based on factors such as oil viscosity and treatment requirements.
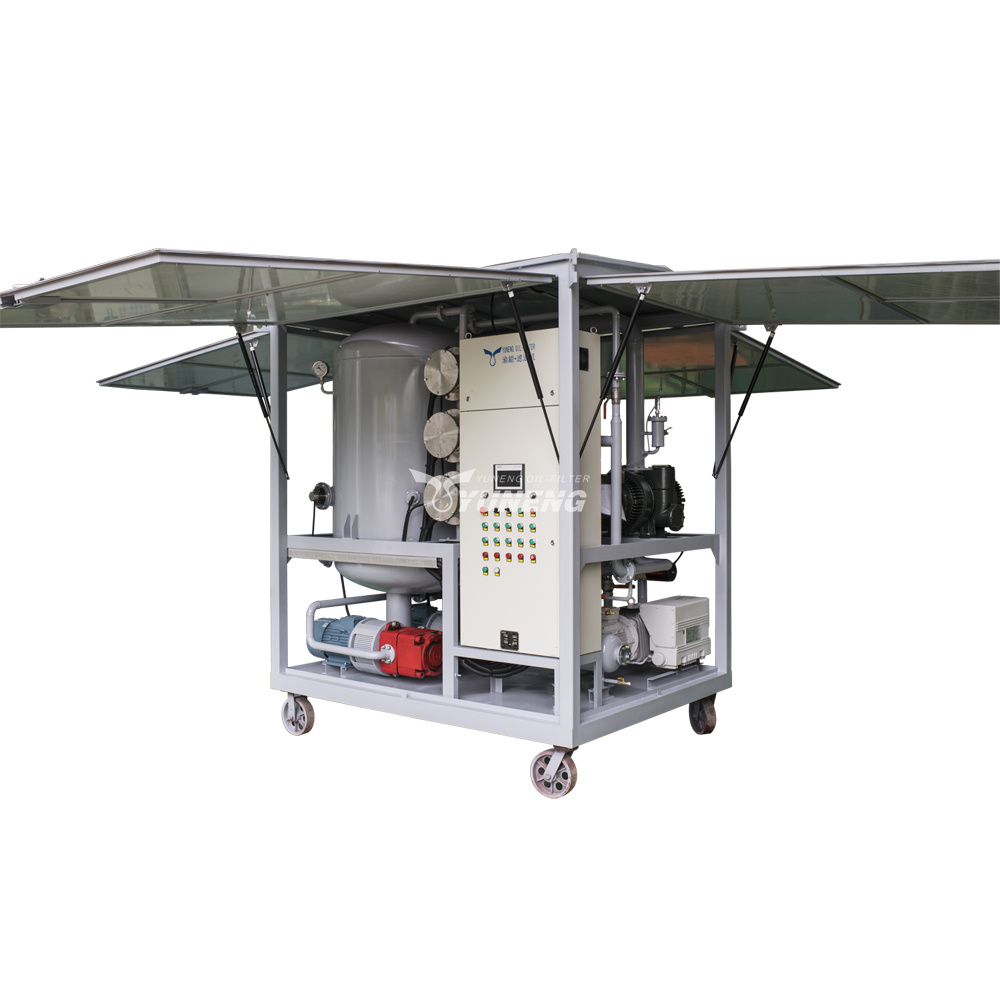
Benefits and Applications of the ZJA Transformer Oil Treatment Plant
Enhanced Transformer Performance and Reliability
- Improved Cooling Efficiency: The ZJA plant removes dissolved gases and moisture from the oil, enhancing its thermal conductivity and promoting efficient heat dissipation from the transformer core and windings. This translates to lower operating temperatures, reduced thermal stress, and improved overall transformer lifespan.
- Strengthened Insulation Properties: By eliminating conductive impurities and moisture, the plant restores the oil’s dielectric strength, minimizing the risk of electrical breakdown and short circuits. This leads to increased insulation reliability and enhanced transformer safety.
- Reduced Operating Costs: Optimized cooling and improved insulation efficiency contribute to lower energy consumption. Additionally, extended oil life minimizes the need for frequent replacements and associated disposal costs.
Extended Oil Life and Environmental Sustainability
- Contaminant Removal: The ZJA plant effectively removes dissolved gases, moisture, and solid particles from the oil, preventing their accumulation and degradation of the oil’s properties. This extends the oil’s service life and reduces the need for premature replacement.
- Reduced Environmental Impact: Extended oil life translates to lower consumption and minimizes the environmental footprint associated with oil production, transportation, and disposal. Additionally, the plant’s energy efficiency further contributes to a more sustainable operation.
Enhanced Safety and Operational Convenience
- Comprehensive Safety Features: The ZJA plant incorporates multiple safety measures, including automatic shutdowns, pressure relief valves, and temperature monitoring systems, minimizing operational risks and protecting both personnel and equipment.
- Automated Control System: The plant features a PLC-based control system that automates various processes, ensuring consistent treatment performance and minimizing operator intervention.
- Remote Monitoring and Data Acquisition (Optional): Integration with a SCADA system enables remote monitoring of plant operation, real-time data analysis, and preventive maintenance scheduling, further enhancing convenience and efficiency.
Versatile Applications
- Pre-commissioning Oil Treatment: Dehydration and degassing of new transformer oil before filling ensures optimal initial performance and extends its lifespan.
- Routine Maintenance: Regular oil purification using the ZJA plant removes contaminants accumulated during operation, maintaining optimal transformer performance and preventing premature degradation.
- Rejuvenation of Degraded Oil: The plant’s advanced treatment capabilities can revitalize aging transformer oil by removing contaminants and restoring its insulating and cooling properties, potentially deferring costly transformer replacements.
Conclusion
The ZJA transformer oil filtration machine is a versatile and reliable solution for maintaining optimal oil conditions in power transformers. Its robust design, advanced functionalities, and comprehensive safety features contribute to enhanced equipment longevity and improved power grid reliability.