Best Practices for Transformer Oil Maintenance in Harsh Environmental Conditions
Table of Contents
Transformers are critical components in power distribution networks, and their performance heavily relies on the condition of their insulating oil. Environmental conditions–such as extreme temperatures, moisture, dust, and chemical contaminants–can accelerate transformer oil degradation, leading to reduced efficiency and potentially equipment failure.
Maintaining transformer oil properly is critical to ensure its reliability and prolong its lifespan, so this article explores causes of oil degradation in extreme environments and provides best practices for keeping transformers running at their optimal level.
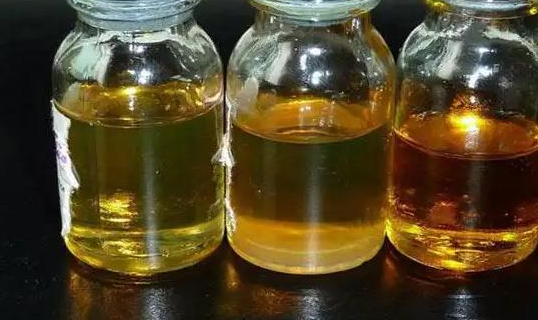
Transformer Oil Degradation in Harsh Environments
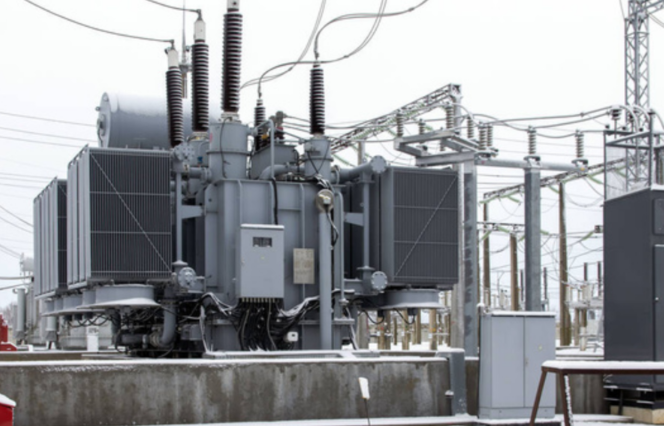
Transformer oil is essential to insulation and cooling in transformers, yet harsh environments can quickly degrade its performance. Key factors contributing to oil breakdown include:
- Oxidation – Long-term exposure to high temperatures and oxygen can form acidic compounds, which compromise efficiency, leading to the formation of sludge and waste products that compromise its efficiency and thus diminish effectiveness.
- Moisture Ingress – Humidity and water contamination decrease dielectric strength while hastening corrosion.
- Thermal Stress – High temperatures hasten chemical degradation while freezing temperatures may lead to oil thickening.
- Contaminants – Dust, dirt, and chemical pollutants found in industrial or coastal environments can clog filters and diminish insulation properties, significantly decreasing insulation properties and making filtration systems inefficient.
- Electrical Stress – Arcing and partial discharges produce harmful gases which deteriorate oil quality, creating electrical tension within a circuit and degrading its quality.
Desert climates present several unique issues; excessive heat and sand infiltration are major concerns, while humid coastal regions must contend with moisture issues. Industrial zones may introduce chemical pollutants while high-altitude locations experience wide temperature swings. Without proper maintenance, degraded oil leads to insulation failure, increased energy losses, and even transformer breakdown.
Proactive monitoring and maintenance are essential to mitigating risks in challenging environments and guaranteeing reliable transformer operation.
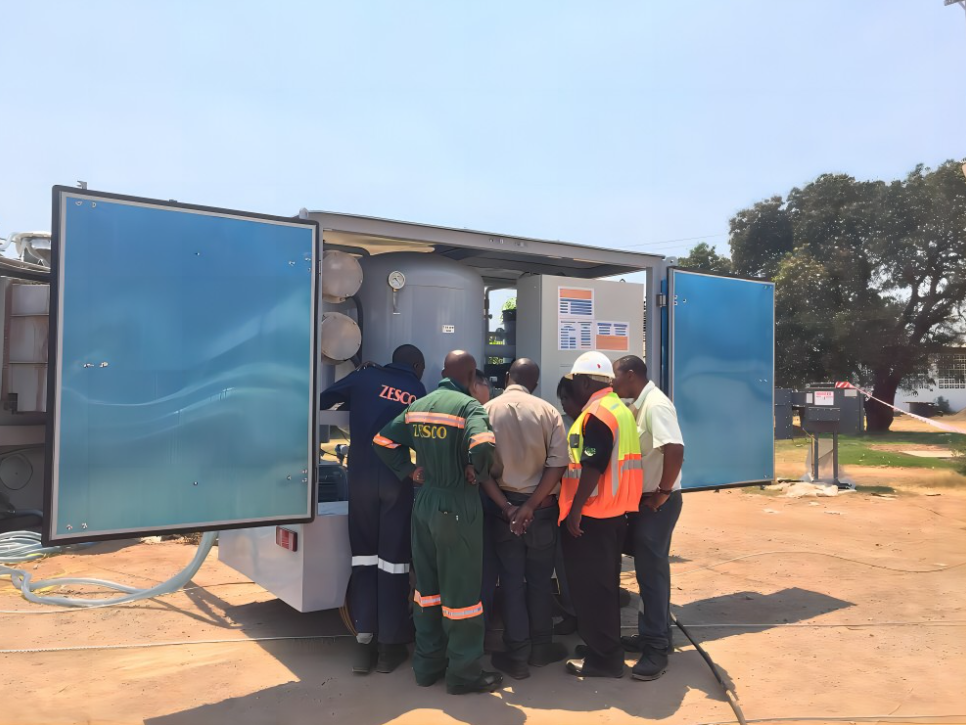
Key Maintenance Practices for Transformer Oil
Protecting transformer oil in extreme environments requires taking proactive steps to prevent early degradation and ensure reliable operation. Exposure to extreme temperatures, humidity, dust, and chemical contaminants can rapidly degrade oil quality, leading to insulation failure, overheating, and costly transformer damage. Implementing best practices helps mitigate these risks and extend both its and its respective transformer’s lifespans.
Regular Oil Testing and Monitoring
Routine oil testing is essential to detecting early signs of degradation and preventing transformer failures in harsh environments where contaminants and extreme operating conditions accelerate oil breakdown, necessitating frequent analyses. Key tests for oil breakdown include:
- Dielectric Strength (BDV) Test – Measures an oil’s ability to withstand electrical stress. A low Breakdown Voltage (BDV) can indicate moisture or particulate contamination that could result in insulation failure; regular BDV tests help identify when purification or replacement measures may be required.
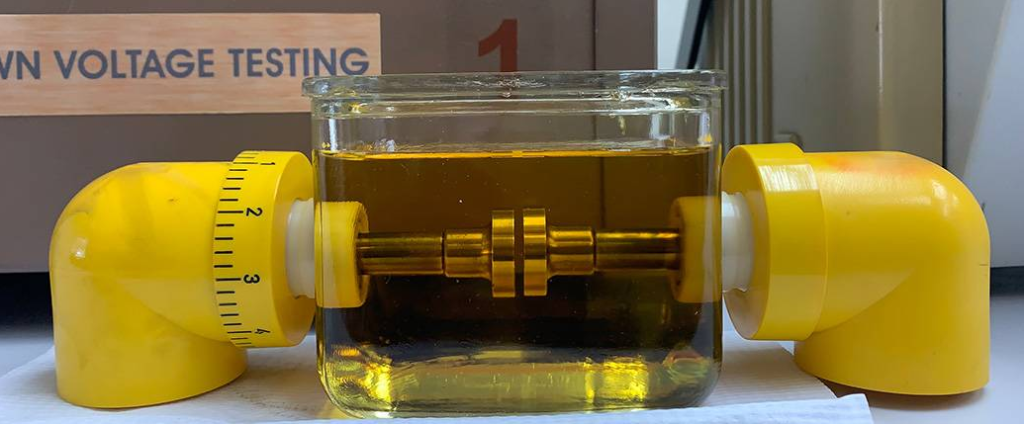
- Acid Number (AN) Test – Measures byproducts of oxidation that accelerate corrosion and sludge formation, decreasing cooling efficiency. An acid number test measures how quickly acidity rises as corrosion accelerates. Rising acidity reduces cooling efficiency as corrosion accelerates and sludge formation increases.
- Moisture Content Test – Determines water ingress, an important issue in humid or fluctuating climates, with excess moisture leading to lower dielectric strength and oil decay.
- Dissolved Gas Analysis (DGA) – DGA detects fault gases like hydrogen, methane, and ethylene, which indicate potential issues within an electrical circuit, such as arcing, overheating, or partial discharge.
Automated monitoring systems allow real-time tracking of oil health, enabling predictive maintenance. By combining lab tests and on-site diagnostics, operators can optimize maintenance schedules and avoid unanticipated breakdowns.
Managing Temperature Extremes
Heat is a major factor in oil degradation. High temperatures accelerate oxidation, while extreme cold can cause viscosity issues. Best practices include:
- Optimizing Cooling Systems – Ensure radiators, fans, and pumps are functioning efficiently.
- Load Management – Avoid overloading transformers in hot climates to reduce thermal stress.
- Thermal Monitoring – Install real-time temperature sensors with alarms for overheating conditions.
- Using High-Temperature Stable Oils – Synthetic or inhibited oils perform better under thermal stress.
Transformer Oil Purification Techniques
Effective purification is key to protecting transformer oil against harsh conditions. Key methods include:
- Filtration – Filtering can remove solid contaminants such as dust and metal particles that damage insulation from reaching their target location.
- Vacuum Dehydration – Evaporates moisture at low pressure, eliminating moisture build-up while simultaneously strengthening dielectric strength.
- Degassing – Removing any dissolved gases (oxygen, nitrogen) to protect against oxidation and gas-induced breakdown.
- Centrifugation – Effectively separates sludge and heavy contaminants for oil that has become heavily polluted.
Modern automated purification systems combine these techniques for continuous maintenance without transformer shutdown. If degradation becomes severe, full oil replacement may be required.
Oil Reconditioning or Replacement
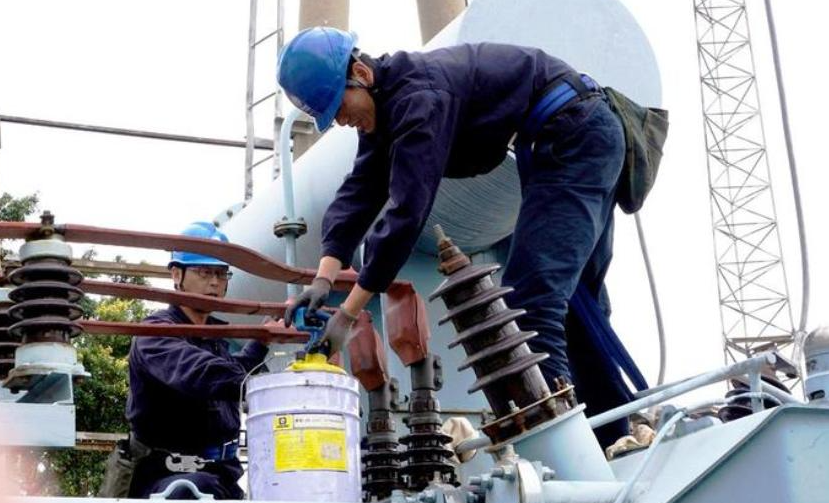
When oil becomes degraded, operators must decide between reconditioning or replacement as their best course of action:
- Reconditioning involves filtering, dehydration and degassing to restore oil properties at an economical price point. Reconditioning may be appropriate for moderately degraded oils.
- When oil has become severely oxidized, sludged or contaminated beyond recovery, replacement becomes inevitable.
Cost-benefit analysis helps determine the optimal course of action – reconditioning extends oil life while replacement ensures reliability in critical applications.
Advanced Transformer Oil Purification Machine for Maintenance
Modern transformer oil purification machines play a critical role in maintaining oil quality in harsh environments. These systems utilize advanced filtration, dehydration, and degassing technologies to remove contaminants, moisture, and gases while returning oil back to optimal condition.
YUNENG, a premier manufacturer of transformer oil purification equipment, provides reliable and cost-effective machines designed for optimal performance. Their machines feature:
- Multi-stage filtration to filter out solid particles and sludge.
- High-efficiency vacuum dehydration for fast moisture removal.
- Degassing modules can extract harmful dissolved gases.
- Automated controls enable precise operation and real-time monitoring.
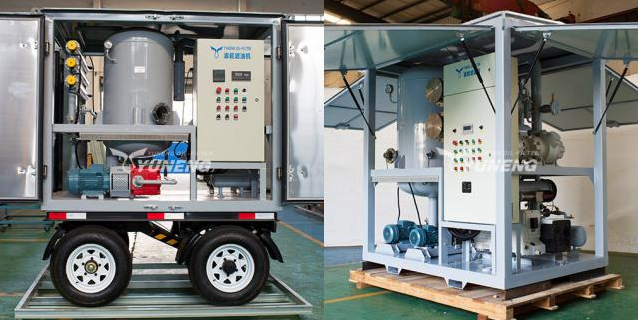
YUNENG oil purification systems are ideal for power utilities and industrial applications, helping extend transformer lifespan while decreasing maintenance costs. Boasting robust construction with energy-saving designs, their machines operate efficiently even under extreme temperatures or polluted environments.
By employing advanced purification technologies like those provided by YUNENG, operators can effectively and proactively maintain transformer oil to prevent failures and optimize performance even under challenging conditions.
Summary
Effective transformer oil maintenance in harsh environments requires regular testing, temperature control, and advanced purification. Modern solutions like YUNENG’s oil purification machines efficiently remove contaminants, moisture, and gases, extending oil life and preventing failures. By adopting these best practices, operators can enhance transformer reliability, reduce downtime, and ensure long-term performance in demanding conditions.