Everything You Need to Know about Vacuum Pump
What are Vacuum Pumps?
Vacuum pumps are mechanical devices that remove gas molecules from a sealed container, creating a partial vacuum. This “partial” distinction is important because a perfect vacuum, completely devoid of any matter, is impossible to achieve in practice.
In simpler terms, vacuum pumps “suck out” air and other gases, creating a low-pressure environment within the sealed chamber. This low-pressure environment is crucial for various industrial, scientific, and everyday applications.
How Does a Vacuum Pump Work?
While the core principle of reducing the volume occupied by gas molecules remains constant, the specific mechanisms employed by different types of vacuum pumps vary significantly. Here’s a more detailed breakdown of two main categories:
1. Positive Displacement Pumps
These pumps operate by mechanically trapping a specific volume of gas and then physically moving it out of the chamber. This creates a lower pressure region behind the trapped volume, drawing more gas into the chamber to fill the void. The cycle continues, progressively reducing the pressure within the chamber.
Here are some common types of positive displacement pumps:
- Piston Pumps: These pumps use a reciprocating piston to trap and compress gas within a cylinder. As the piston retracts, it increases the volume within the cylinder, drawing in gas from the chamber. The forward stroke then compresses the trapped gas and pushes it out through an exhaust valve.
- Rotary Vane Pumps: These pumps utilize a rotating shaft with vanes that slide within a slotted housing. As the shaft rotates, the vanes trap pockets of gas between the housing and the rotor. The rotation further compresses the trapped gas and eventually releases it through an exhaust port.
- Screw Pumps: These pumps employ intermeshing helical screws that rotate within a casing. The meshing action traps pockets of gas between the screw threads and the casing. The rotation then moves the trapped gas along the screw flutes, compressing it and ultimately discharging it through an exhaust port.
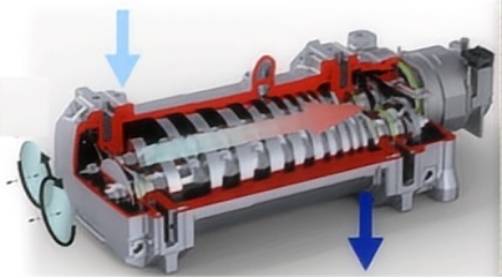
2. Momentum Transfer Pumps
These pumps don’t physically trap gas but instead rely on transferring momentum to gas molecules, pushing them out of the chamber. This creates a directed flow of gas molecules, effectively reducing the overall pressure within the chamber.
Here are some prominent examples of momentum transfer pumps:
- Diffusion Pumps: These pumps utilize high-speed jets of oil vapor directed towards the chamber. The oil vapor molecules collide with gas molecules, transferring momentum and pushing them towards the pump’s exhaust. The oil vapor itself is continuously replenished and separated from the pumped gas through a complex system of baffles and condensation traps.
- Turbo Molecular Pumps: These pumps employ high-speed turbine blades that rotate at very high speeds (up to several hundred thousand RPM). Gas molecules colliding with these blades transfer momentum and are directed towards the pump’s exhaust. Unlike diffusion pumps, turbo molecular pumps operate without oil, making them cleaner and requiring less maintenance.
Key Points to Remember:
- Positive displacement pumps are generally better suited for achieving rough vacuum (higher pressure ranges) and are known for their simplicity and reliability.
- Momentum transfer pumps are more effective at reaching high vacuum (lower pressure ranges) but are often more complex and require specialized expertise for operation and maintenance.
The choice between these categories, and specific pump types within each category, depends on the desired vacuum level, application requirements, operating environment, and budget.
Where are Vacuum Pumps Used?
The diverse capabilities of vacuum pumps have led to their widespread use across numerous industries. Here are some prominent examples, with a particular focus on the application of vacuum pumps in transformers:
1. Semiconductor and Electronics Industry: Vacuum pumps are essential for manufacturing microchips and other electronic components by creating a clean and dry environment free from contaminants like air and moisture.
2. Food and Beverage Industry: Vacuum packaging utilizes pumps to remove air from containers, extending the shelf life of food products and preventing spoilage.
3. Chemical Industry: Vacuum pumps play a vital role in various chemical processes, including distillation, evaporation, and degassing.
4. Medical Field: Vacuum technology is crucial in medical equipment like vacuum pumps used in laboratories, freeze dryers for preserving blood plasma and other biological materials, and suction devices during surgical procedures.
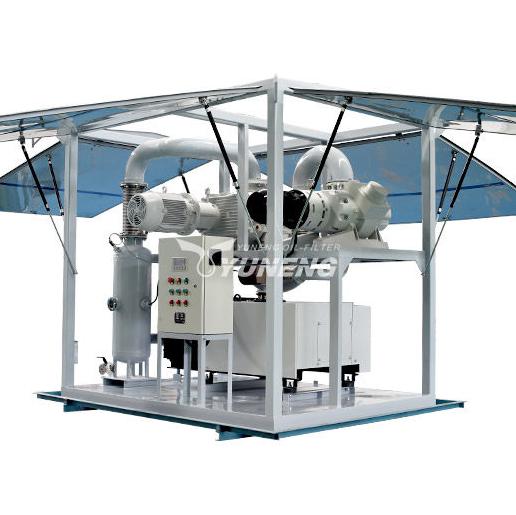
5. Power Transmission and Distribution: Vacuum pumps play a critical role in maintaining the health and efficiency of transformers, which are essential components in the electrical grid. Here’s a detailed breakdown of their function in transformers:
- Transformer Oil Degassing: During transformer operation, the insulating oil can absorb moisture and air over time. This can lead to electrical breakdowns and reduced transformer lifespan. Vacuum pumps are used in a process called transformer oil degassing. In this process, the oil is heated and exposed to a vacuum created by the pump. The vacuum facilitates the removal of dissolved gases and moisture from the oil, improving its insulating properties and extending transformer life.
- Transformer Drying: New transformers or transformers undergoing repairs may contain moisture trapped within the insulation materials. This moisture can also lead to electrical problems. Vacuum pumps are employed in a process called transformer drying. Here, the transformer is evacuated, and the low pressure promotes the evaporation of moisture from the insulation materials. This drying process ensures the transformer operates efficiently and safely.
6. Other Applications:
Vacuum pumps are also employed in diverse applications like:
- Coating various materials with thin films
- Incandescent and fluorescent lamp manufacturing
- Heating, ventilation, and air conditioning (HVAC) systems
- Leak detection
What is a Two Stage Vacuum Pump?
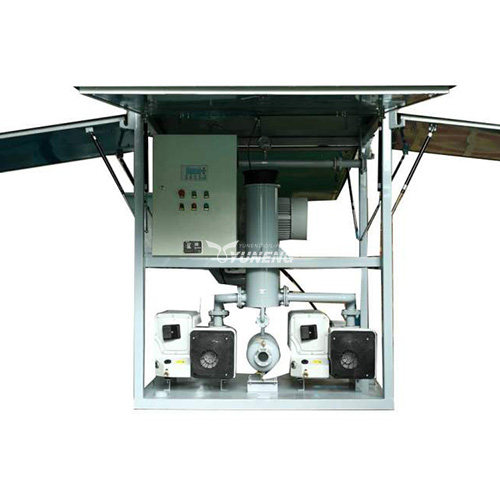
A two-stage vacuum pump design is a type of vacuum pump commonly used in industrial applications where ultra-high vacuum (UHV) levels are required. This design consists of two sets of rotors and vanes, enabling it to operate in two distinct stages: a low vacuum stage and a high vacuum stage.
Here’s a more detailed explanation of how a two-stage vacuum pump works:
- Low Vacuum Stage: In the first stage, the pump operates at a relatively low vacuum level. Process gas is initially drawn into the pump through the inlet port. As the rotors rotate, the gas is compressed and transferred to the second stage of the pump.
- High Vacuum Stage: In the second stage, the gas from the first stage is further compressed to achieve higher vacuum levels. The second set of rotors and vanes operate at higher speeds and tighter tolerances, allowing for more efficient compression of the gas. The gas is compressed to atmospheric pressure or close to it, significantly improving the vacuum performance of the pump.
By utilizing two stages, each optimized for different pressure ranges, a two-stage vacuum pump can achieve deeper vacuum levels and better overall performance compared to single-stage pumps. This makes them particularly suitable for applications where extremely low pressures are necessary, such as in semiconductor manufacturing, thin film deposition, analytical instrumentation, and various research and industrial processes.
Key advantages of a two-stage vacuum pump design include:
- Deeper Vacuum Levels: The two-stage configuration allows for more efficient compression of gas, enabling the pump to achieve deeper vacuum levels than single-stage pumps.
- Improved Performance: By separating the compression process into two stages, the pump can achieve better overall performance in terms of vacuum level and pumping speed.
- Versatility: Two-stage vacuum pumps are versatile and can handle a wide range of applications requiring different vacuum levels.
However, it’s essential to note that two-stage vacuum pumps may be more complex and expensive than single-stage pumps due to their dual-stage design. Additionally, proper maintenance and care are crucial to ensure optimal performance and longevity of the pump.
What is the Lifespan Cost of a Vacuum Pump?
The most expensive component in the lifespan cost of a vacuum pump is its energy consumption. In fact, a vacuum pump’s energy consumption typically costs five times more than its purchase price over the pump’s lifespan while maintenance costs are about 30%.
- Initial Purchase Price (10%): This refers to the upfront cost of acquiring the vacuum pump. It accounts for 10% of the total cost.
- Maintenance Cost (30%): Maintenance costs include routine servicing, repairs, and any replacement parts needed to keep the vacuum pump operational over its lifespan. This typically amounts to 30% of the total cost.
- Energy Consumption (50%): Energy consumption is the most significant cost factor, representing 50% of the total cost. This includes the electricity or other energy sources required to power the vacuum pump during its operation.
- Additional Expenses (10%): This category covers any other miscellaneous expenses associated with the vacuum pump that are not accounted for in the initial purchase price or maintenance costs. It represents 10% of the total cost.
Given that energy consumption accounts for 50% of the total cost and is the most significant expense over the vacuum pump’s lifespan, it’s crucial to prioritize energy efficiency when selecting a vacuum pump system. By choosing a more energy-efficient and reliable system, you can reduce the total cost of ownership significantly.
To minimize energy consumption and overall costs, you should consider factors such as the pump’s design, efficiency ratings, operating conditions, and any available energy-saving features. Regular maintenance and proper operation are also essential to ensure optimal performance and efficiency, thereby reducing energy consumption and extending the lifespan of the vacuum pump.
In summary, while the initial purchase price and maintenance costs are significant considerations, the energy consumption of the vacuum pump represents the most substantial portion of the total cost over its lifespan. Prioritizing energy efficiency and reliability can lead to significant cost savings in the long run.
What is the Vacuum Pump for a Transformer?
Transformer vacuum pumps, though less ubiquitous than their industrial counterparts, play a critical role in safeguarding the efficiency and longevity of transformers, the workhorses of electrical power transmission and distribution. Here’s a closer look at these specialized pumps and their importance:
The Role of Transformer Oil
Transformers rely on a special type of insulating oil for several crucial functions:
- Electrical Insulation: The oil acts as a barrier between high-voltage windings, preventing electrical current from arcing and causing damage.
- Heat Transfer: The oil absorbs heat generated by the transformer’s operation, facilitating efficient heat dissipation and preventing overheating.
The Threat of Degradation
Over time, transformer oil can degrade due to exposure to:
- Oxygen: Oxygen reacts with the oil, leading to the formation of sludge and acids that can compromise its insulating properties.
- Moisture: Water vapor can dissolve in the oil, reducing its electrical insulation strength and potentially causing electrical breakdowns.
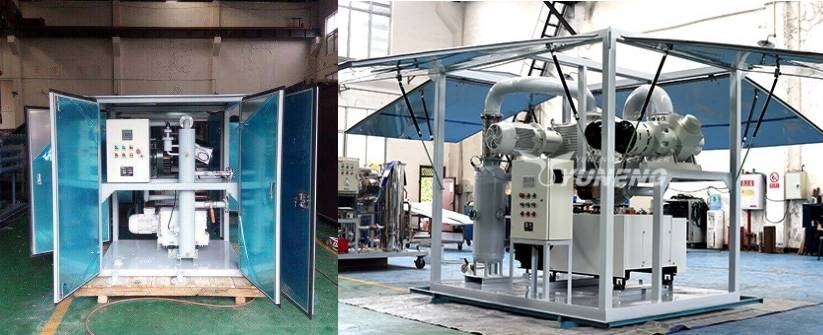
How do Transformer Vacuum Pumps Come to the Rescue?
Transformer vacuum pumps are employed during transformer maintenance and repair processes to remove air and moisture from the insulating oil. This critical procedure offers several benefits:
- Prevents Oil Degradation: By removing oxygen and moisture, the pump helps maintain the oil’s insulating properties and slow down its degradation.
- Extends Transformer Lifespan: Preserving the integrity of the oil directly translates to a longer lifespan for the transformer itself.
- Reduces Maintenance Costs: By preventing premature oil breakdown, transformer vacuum pumps help minimize the need for frequent oil replacements, lowering overall maintenance costs.
The Pump of Choice: Rotary Vane Pumps
Transformer vacuum pumps typically utilize rotary vane pumps. Here’s why they’re well-suited for this application:
- Simplicity: Rotary vane pumps offer a robust and relatively simple design, making them reliable and easy to maintain in the field.
- High Flow Rates: These pumps can handle large volumes of gas efficiently, crucial for quickly removing air and moisture from transformers, often containing significant oil volumes.
- Durability: Rotary vane pumps are known for their durability, able to withstand the demands of continuous operation during transformer maintenance procedures.
The Process of Transformer Oil Dehydration
The process of using a vacuum pump for transformer oil dehydration typically involves these steps:
- Oil Filtration: The oil is passed through filters to remove any solid contaminants.
- Heating: The oil is gently heated to facilitate the removal of moisture.
- Vacuum Pumping: The transformer vacuum pump is connected to the oil system, and the pump removes air and moisture from the heated oil.
- Monitoring and Dehydration: The process is closely monitored, and the pump continues to operate until the desired level of dehydration is achieved.
Transformer vacuum pumps, though a specialized application within the broader world of vacuum technology, play a vital role in ensuring the smooth and efficient operation of the electrical grid. By safeguarding the integrity of transformer oil, these pumps contribute significantly to the reliable transmission and distribution of electrical power.
The YUNENG ZJ Series Vacuum pump units are extensively utilized for highly efficient vacuum drying and suction processes during the installation and maintenance of large transformers. These units are particularly well-suited for vacuum operations in substations, transformer manufacturing plants, and power plants.
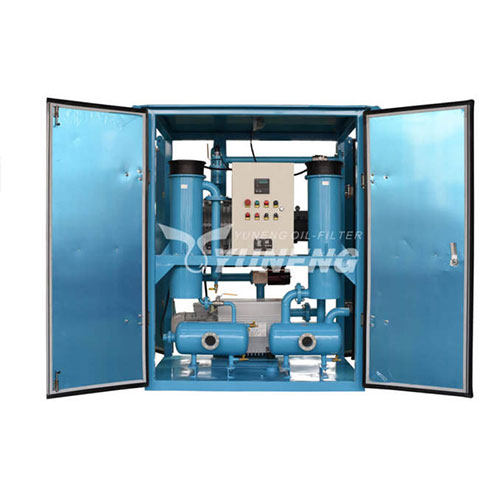
Our product range includes models with varying capacities, such as 1000m³/h, 2000m³/h, 500m³/h, and 150m³/h, among others. You can select the model that best suits your specific requirements and operational needs.
If you have any interest in our products or services, do not hesitate to contact us.