Why Wind Farms Need High-Efficiency Transformer Oil Filtering Machines
Wind farms depend on power transformers to increase voltage for long-distance energy transmission, yet contaminated insulating oil can cause insulation failures, overheating, and potentially devastating blowouts that suspend operations and drain budgets. Since turbines are often located in remote and inhospitable locations, keeping the oil clean becomes a difficult task.
Transformer oil filtration machine address this problem directly. By stripping out moisture, sludge, and microscopic particles, they help to lengthen the transformer’s working life, lower routine maintenance expenses, and safeguard continuous power delivery.
Table of Contents
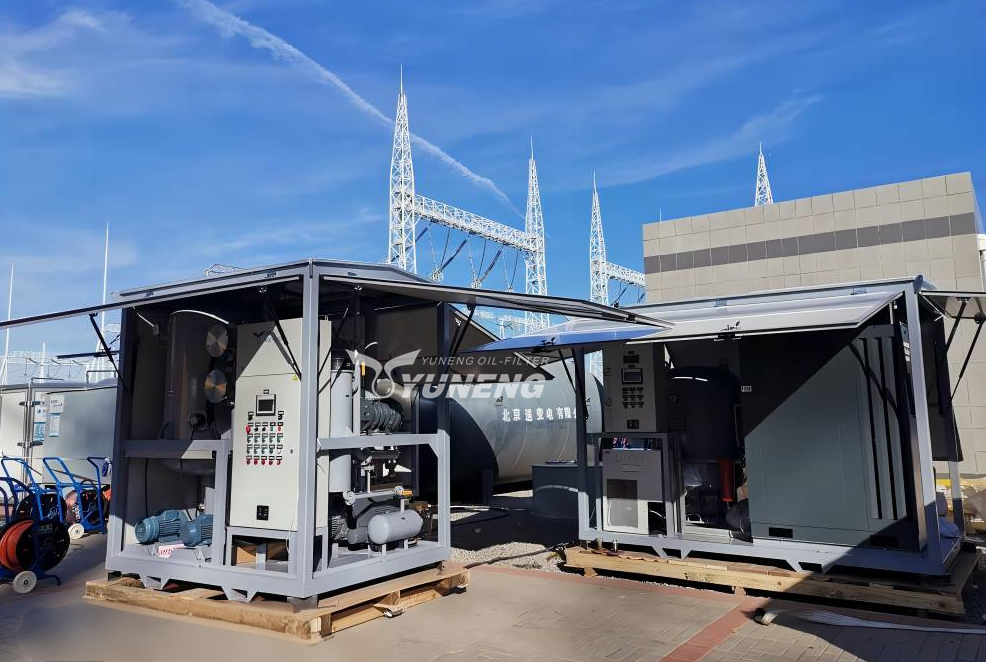
The Importance of Purifier Transformer Oil in Wind Farms
Transformer oil works like blood for the power transformers at wind farms; it keeps the whole system running cool and steady. Its main jobs are to insulate wires, pull heat away from hotspots, and guard against rust, and all three keep the transformers healthy.
Out in wind parks, where the units sit far away in wind-swept fields, that oil faces a rough life. Moisture, wide temperature swings, and bits of dirt settle in and speed up the oils’ breakdown. Dirty oil lets sludge form, clogs cooling paths, and wears down coils and seals long before they should. If nobody steps in, those problems force budget-wrecking repairs and power cuts that stop turbines from earning money.
Passing the oil through top-grade filters pulls out water, gases, and tiny debris so it can work like new again. Cleaner oil lasts longer, insulates better, and leaves internal metal surfaces free from corrosive attack. For wind-farm managers, a little time and money spent on purification beats the big bills of early replacements or full transformer rebuilds.
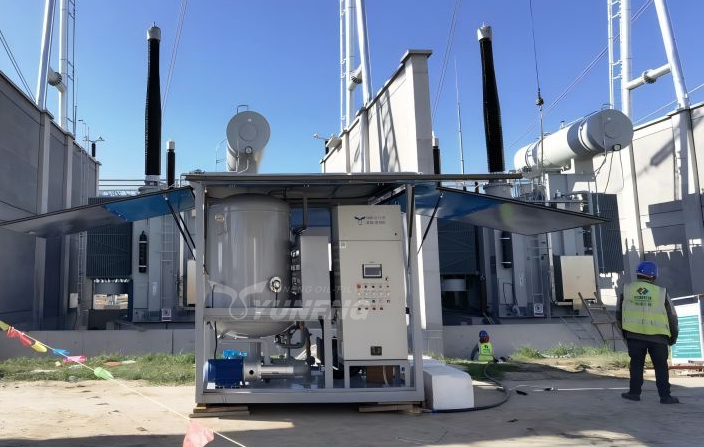
Key Features of the Best Transformer Oil Filtration Systems for Wind Farm
Picking the right transformer oil filtration machine for a wind farm means looking for features that guarantee steady operation, solid performance, and simple upkeep. The four key abilities listed here capture what matters most.
Advanced Multi-Stage Filtration
A first-rate unit uses multi filtering stages in a row-usually coarse removal, fine screens down, and a final pass through activated carbon or resin. The coarse stage catches large bits and sludge, so the later filters stay clean longer. Fine mesh or depth cartridges grab tiny particles that lower dielectric strength and speed up aging. At the end, polishing media pull out oxidation leftovers and dissolved acids, bringing the oil close to new again. This stepped plan keeps more contaminants out and stretches the time between service trips.
Integrated Vacuum Dehydration & Degassing
Water and trapped gas cause partial discharge, raise heat, and tear down paper insulation. The best machines have a vacuum chamber running under 10 mbar, where oil is slowly warmed to 60 to 80 °C. Because of the vacuum, water boils off at a mild temperature, and gases rise out of solution. A molecular sieve or cold trap then catches the escaping moisture. The end product sits below 5 ppm water and nearly zero dissolved gas, fully restoring dielectric punch.
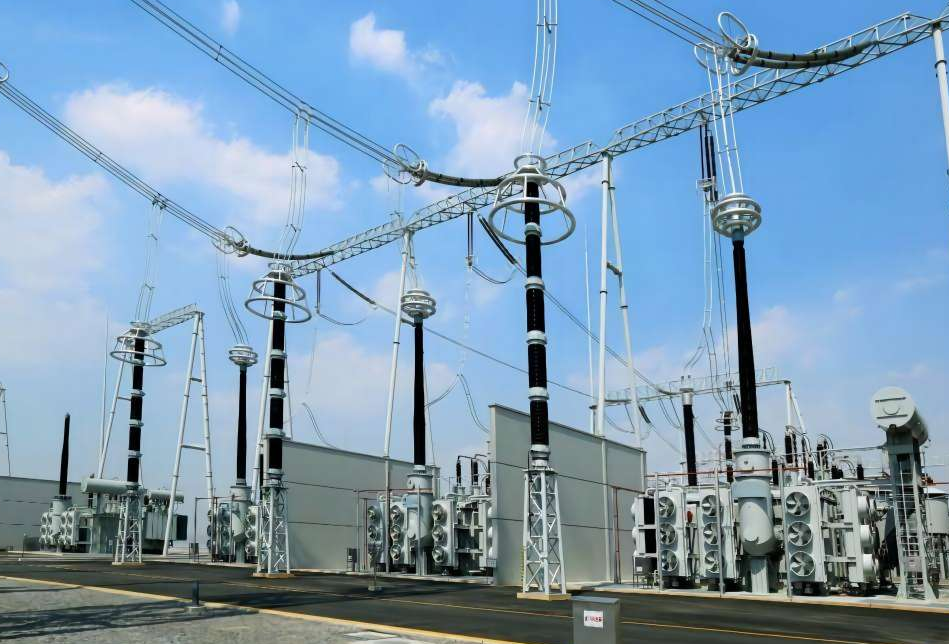
Portable, Ruggedized Design for Remote Sites
Most wind farms are planted on gusty mountaintops or way out at sea, which makes getting heavy equipment to the job a real headache. That is why some portable transformer oil filtering machine rolls in on a tough skid frame or pulls behind a trailer, both coated in anti-corrosion paint, and fitted with big wheels or forklift pockets. A noise-quiet cover and fully weather-sealed shell guard the pumps, controls, and electrical guts. Quick-release hoses and built-in lifting rings make set-up fast, and cartridge filter cans snap out on the spot with no special tools.
Automation & Remote Monitoring Capabilities
To take the strain off technicians and cut mistakes, new models come with PLC or microprocessor brains that run preset filter cycles and lock out power when things go wrong. A bright touchscreen shows flow speed, moisture at the inlet and outlet, vacuum pressure, and how much dirt is already trapped. Plenty of units now speak IoT: they ping a team member by text or e-mail the moment particles spike or a cartridge change comes due. That heads-up keeps wind-farm transformers clean while spending as little time and staff onsite as possible.
Cost-Benefit Analysis: Transformer Oil Filtration Machine vs. Replacement
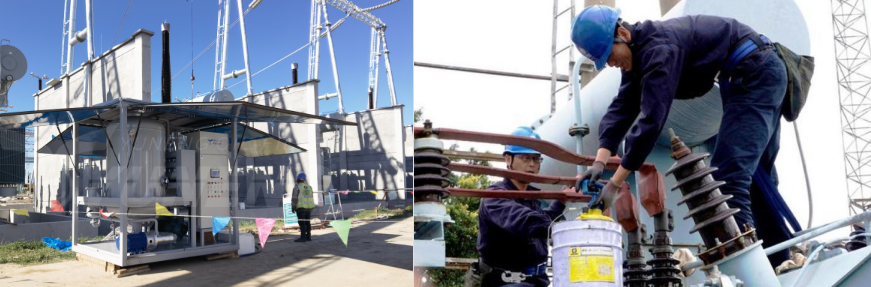
When managing wind farm assets, budget optimization and operational continuity are key priorities. One critical decision point is whether to replace degraded transformer oil entirely or to restore it using a transformer oil filtration machine.
At first glance, a full oil change sounds appealing. The reality, however, is a snarl of logistics and red tape. Hundreds of liters of waste must be pumped, transported, and disposed of by strict environmental rules. Even after all that work, fresh oil quickly picks up moisture, oxygen, and gas pockets, especially in remote or offshore sites.
Filtration, by contrast, cleans and refreshes the original batch, boosting dielectric strength and chemical balance without trucking away toxic waste. Modern, high-flow skid-mounted units can usually run right on-site, letting turbines keep turning and crews finish routine tasks with only a brief pause.
Frequent swaps also throw internal parts into a yo-yo of heat and chemistry, often speeding fatigue through the winding and bushings. A steady filtration schedule, however, steadies those variables and gives long-term protection to the overall system.
Here’s a quick comparison to illustrate the practical differences:
Aspect | Oil Replacement | Transformer Oil Filtration |
Environmental Impact | High (oil disposal required) | Low (oil reused) |
Downtime Required | Significant | Minimal or none |
Cost Efficiency | High recurring expense | Lower operating cost over time |
Operational Disruption | Requires full system shutdown | Can often run inline or during partial operation |
Long-Term Equipment Wear | Risk of fluctuation-related stress | Stable operating conditions preserved |
In a word, filtration is a smarter, more sustainable solution for wind farms focused on performance and cost control.
To Sum Up
Wind turbines count on the seamless run of their transformers to deliver constant output. Transformer oil deteriorates with the passage of time, weakening these systems. That’s why a high-efficiency transformer oil filter machine is a better alternative to good maintenance – it’s a proactive approach to securing long-term performance.
With advanced transformer oil filtration equipment, wind farm operators are able to remove harmful contaminants, extend transformer lifespan, reduce downtime, and save on maintenance costs. Compared to full oil replacement, filtration is less environmentally intrusive, cost-effective, and efficient.
In short, possessing clean, productive oil and a quality transformer oil filtering machine is the key to maximizing the performance of wind farms and protecting essential equipment.
If you are interested in an oil purification machine for your power system, YUNENG is a good choice. Get in touch with us to learn more.