Integrating Transformer Dry Air Machines with Other Maintenance Systems
Maintaining the health and longevity of transformers is crucial for ensuring reliable and efficient power transmission. Moisture is a significant enemy of transformers, as it can degrade insulation, accelerate aging, and lead to catastrophic failures. To combat this threat, transformer dry air machines have emerged as a valuable tool. However, their true potential can be unlocked by integrating them with other crucial transformer maintenance systems.

Importance of Dry Air in Transformer Maintenance
Moisture is a silent enemy lurking within transformers, posing a significant threat to their health and longevity. Its presence can originate from various sources, including:
- Ambient air: Even minute amounts of moisture in the surrounding air can infiltrate the transformer through small openings, seals, or during maintenance activities.
- Leaks: Deterioration of gaskets, seals, or weld points can create avenues for moisture ingress, leading to localized problems or widespread contamination.
- Insulation degradation: Over time, insulating materials like paper and pressboard can absorb moisture from the surrounding environment or through chemical breakdown, increasing their conductivity.
The detrimental effects of moisture on transformers are multifaceted:
- Reduced dielectric strength: Water molecules dissolve in transformer oil, reducing its ability to resist electrical current. This increases the risk of electrical breakdowns, arcing, and potentially catastrophic failures.
- Corrosion of metal components: Moisture promotes the corrosion of metal parts within the transformer, such as windings, tanks, and cooling systems. This weakens structural integrity and can lead to component failures.
- Accelerated degradation of insulating paper: Paper insulation, a critical component in many transformers, readily absorbs moisture, leading to swelling and loss of mechanical strength. This can cause short circuits and ultimately, transformer failure.
While traditional methods like nitrogen purging aimed to mitigate moisture ingress, they have limitations:
- Passive approach: Nitrogen purging simply replaces the transformer’s atmosphere with dry nitrogen, but it doesn’t actively remove moisture already present within the transformer.
- Time-consuming and labor-intensive: The purging process requires significant time and effort, often involving specialized equipment and skilled personnel.
- Limited effectiveness: Repeated purging may be necessary, as it doesn’t address ongoing moisture ingress from leaks or insulation degradation.
Therefore, a more proactive and effective approach to moisture control is essential. This is where transformer dry air machines emerge as a valuable solution.
What are the Working Principles of Transformer Dry Air Machines?
Transformer dry air machines operate on a fundamental principle: actively lowering the moisture content of the air within the transformer to an extremely low dew point, typically ranging below -40°C. This ultra-dry environment effectively prevents moisture condensation and shields the transformer from its detrimental effects. Compared to traditional moisture control methods like nitrogen purging, transformer dry air machines offer several distinct advantages:
1. Continuous Moisture Removal
- Unlike nitrogen purging, which acts as a one-time replacement of the transformer’s atmosphere, transformer dry air machines function continuously. They actively remove moisture present within the transformer, not just replacing it with dry air. This ensures sustained protection even under changing environmental conditions or potential leaks.
- This continuous removal process combats both existing moisture and ongoing ingress, offering superior protection compared to the temporary dryness provided by purging.
2. Enhanced Energy Efficiency
- Modern transformer dry air machines often leverage advanced technologies like desiccant rotors or membrane dryers. These technologies work by physically adsorbing or selectively permeating moisture from the air, requiring significantly less energy compared to the traditional method of nitrogen purging.
- This energy efficiency translates to cost savings for operators and reduced environmental impact due to lower electricity consumption.
3. Environmentally Friendly Operation
- Nitrogen, commonly employed in purging, is a greenhouse gas with a significant environmental footprint. Its production and release contribute to climate change.
- Transformer dry air machines, conversely, operate without relying on nitrogen. They either utilize ambient air or recycle internally dried air, resulting in a more sustainable and environmentally conscious approach to transformer maintenance.
4. Additional Benefits
Besides the core advantages highlighted above, transformer dry air machines offer further benefits:
- Improved transformer lifespan: By proactively mitigating moisture-related damage, transformer dry air machines contribute to longer transformer life expectancy, reducing replacement costs and downtime.
- Enhanced reliability: Consistent moisture control reduces the risk of transformer failures, ensuring stable and reliable power transmission.
- Cost-effectiveness: While the initial investment might be higher than purging, the long-term cost savings on energy, maintenance, and transformer replacement often outweigh the initial cost.
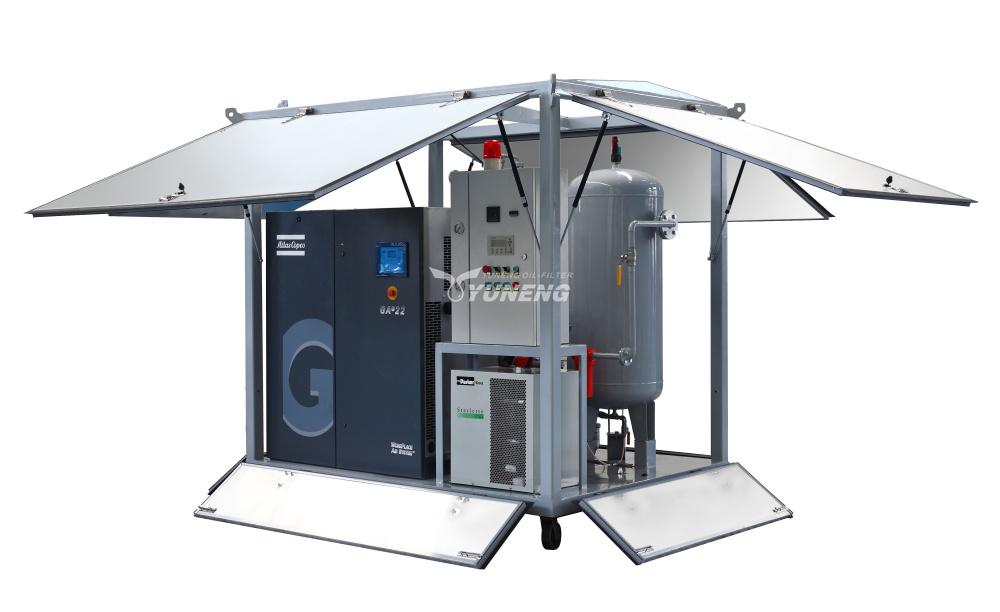
Unlocking Synergy: Integrating Transformer Dry Air Machines with Other Systems
The integration of transformer dry air machines with other crucial maintenance systems unlocks a new level of efficiency and efficacy in transformer care. By working in concert, these systems address moisture-related issues from multiple angles, exceeding the capabilities of each standalone solution. Here are some key integration examples:
1. Oil Filtration Systems
- Challenge: During filtration, even small amounts of moisture in the air can re-contaminate the purified transformer oil, compromising its insulating properties and accelerating degradation.
- Solution: transformer dry air machines continuously dry the air used in the filtration process, ensuring a consistently dry environment. This prevents moisture re-contamination, guaranteeing optimal insulating properties and extending oil life, reducing maintenance costs and downtime.
2. Vacuum Dehydration Systems
- Challenge: While vacuum dehydration removes large volumes of trapped moisture, residual moisture can still be present after the process.
- Solution: Combining transformer dry air machines with vacuum dehydration creates a powerful two-step approach. Vacuum removes bulk moisture, followed by transformer dry air machines actively maintaining a very low dew point, preventing further moisture ingress and ensuring optimal dryness.
3. Dissolved Gas Analysis Systems
- Challenge: Moisture can interfere with dissolved gas analysis readings, potentially masking critical fault indicators like incipient electrical faults or overheating.
- Solution: Transformer dry air machines ensure accurate dissolved gas analysis readings by eliminating moisture interference. This enables early detection of issues related to moisture and other problems, allowing for timely corrective actions and preventing potential transformer failures.
4. Online Monitoring Systems
- Challenge: Traditional methods require manual monitoring of dew point and other key parameters, which can be time-consuming and inefficient.
- Solution: Modern transformer dry air machines seamlessly integrate with online monitoring systems, providing real-time data on the dew point, airflow, and other critical parameters. This enables remote monitoring of transformer health, allowing for predictive maintenance based on data-driven insights and timely intervention if needed, minimizing downtime and improving operational efficiency.
5. Control and Automation Systems
- Challenge: Manual operation of transformer dry air machines can be labor-intensive and may not always adapt to changing transformer conditions.
- Solution: Integrating transformer dry air machines with control and automation systems allows for automated operation based on predefined parameters and real-time data. This ensures optimal drying based on the transformer’s specific needs and operating conditions, optimizing energy consumption and minimizing manual intervention.
Beyond these key integrations, the benefits of synergy extend further:
- Reduced maintenance costs: By proactively addressing moisture-related issues, integrated systems minimize the need for reactive repairs and replacements, leading to significant cost savings.
- Enhanced transformer lifespan: Consistent moisture control and improved fault detection contribute to longer transformer life expectancy, reducing replacement costs and ensuring reliable power delivery.
- Improved operational efficiency: Automation and data-driven insights optimize resource utilization and maintenance schedules, leading to increased operational efficiency and reduced downtime.
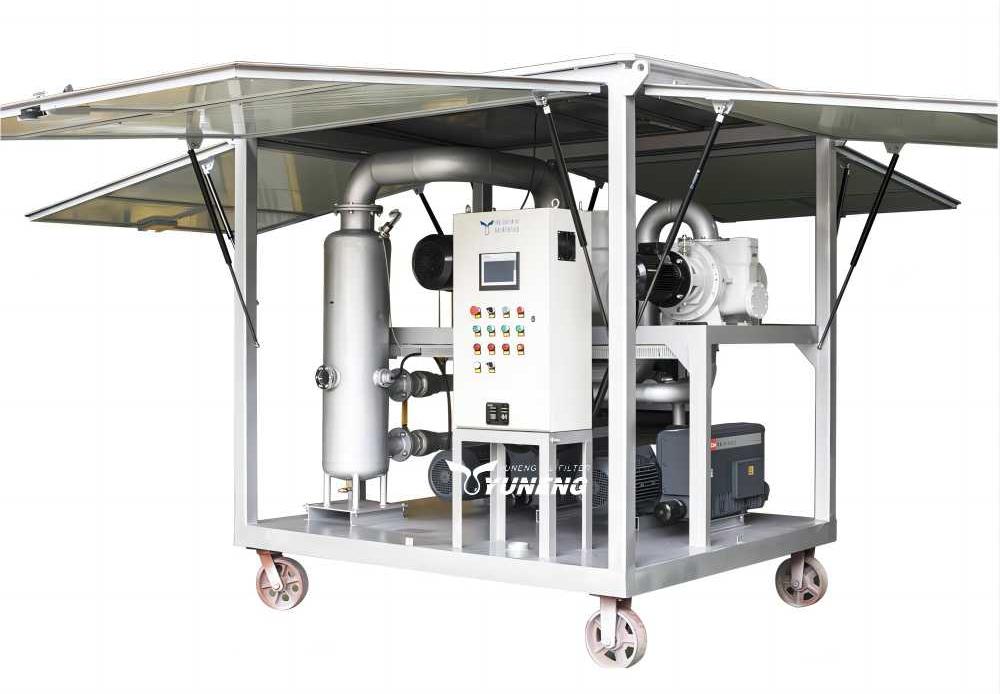
Challenges and Considerations in Transformer Dry Air Machine Integration
While integrating transformer dry air machines with other maintenance systems unlocks significant benefits, it’s crucial to acknowledge and address certain challenges:
1. Compatibility
Seamless communication and data exchange between diverse systems can be complex. Careful planning and consideration of communication protocols are paramount. This includes:
- Identifying compatible protocols: Different systems may employ various data exchange formats and communication standards. Compatibility needs to be established to ensure smooth information flow.
- Standardization and adaptation: Implementing standardized protocols within the integrated system can simplify communication and data management. However, adapting legacy systems to comply with new standards might be necessary in some cases.
2. Complexity
Installation and integration can be intricate, particularly with older systems. This complexity stems from:
- Physical integration: Combining different systems physically within the transformer environment can require space considerations and potential modifications to existing equipment.
- Software integration: Merging the software platforms of individual systems into a cohesive operating environment can be technically challenging, requiring specialized expertise.
3. Cost
The initial investment in integrating transformer dry air machines with other systems may be higher compared to standalone solutions. This includes:
- Hardware costs: New equipment, sensors, and communication infrastructure might be needed for integration.
- Software costs: Licensing and customization of software platforms to facilitate coordinated operation can add to the initial investment.
- Installation and training costs: Specialized expertise for installation and personnel training can contribute to the initial cost.
4. Training and Maintenance
Integrating systems necessitates training personnel on their combined operation and maintenance procedures. This includes:
- Understanding the integrated system: Personnel need to grasp how the individual systems interact and function within the integrated environment.
- Learning new procedures: Operating and maintaining the integrated system might involve new protocols and tasks compared to standalone systems.
- Continuous learning: As technology evolves, ongoing training might be necessary to keep personnel updated on the latest practices and advancements.
However, it’s important to remember that while challenges exist, they can be effectively addressed through:
- Thorough planning and feasibility studies: Carefully assessing the project scope, compatibility issues, resource requirements, and expected benefits can help mitigate challenges and maximize returns on investment.
- Seeking experienced professionals: Collaboration with skilled engineers, technicians, and IT specialists can ensure smooth integration, system efficiency, and proper training.
- Leveraging available resources: Consulting industry best practices, technical manuals, and manufacturer support can provide valuable guidance and troubleshooting assistance.
By acknowledging and proactively addressing these challenges, transformer owners can reap the full benefits of integrated transformer dry air machine systems, ultimately fostering safer, more reliable, and cost-effective transformer operations.
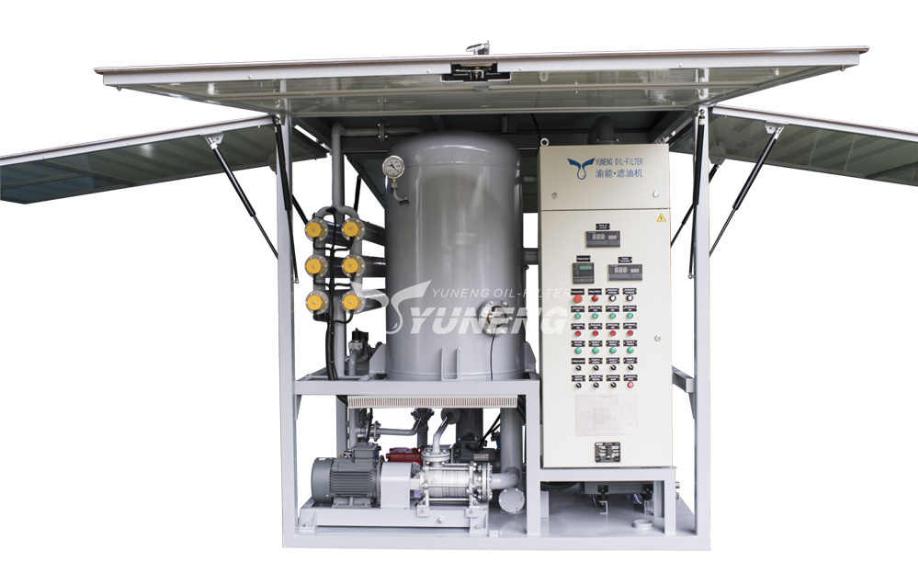
Conclusion
As the demand for reliable and sustainable energy grows, the importance of transformer health and longevity becomes paramount. Integrating transformer dry air machines with other crucial maintenance systems represents a powerful strategy to achieve this goal. By proactively removing moisture and fostering a dry environment, these integrated systems empower us to protect transformers from the damaging effects of moisture, ensuring their optimal performance and extending their lifespan.