Hydraulic Oil Filtration Machines: Basic Things to Know
In the heart of countless industrial applications, hydraulic systems play a vital role in transmitting power and controlling machinery. The lifeblood of these systems is hydraulic oil, a lubricant that facilitates smooth operation and protects components from wear and tear. However, hydraulic oil filtration machines are essential for maintaining oil cleanliness and preventing system degradation. Contamination of hydraulic oil with impurities like dirt particles, metal shavings, moisture, and oxidation byproducts can have severe consequences. These contaminants can increase friction, accelerate wear on components, and lead to malfunctions or even complete system failure. Hydraulic oil filtration machines offer a robust solution to these challenges, ensuring optimal system performance and longevity.
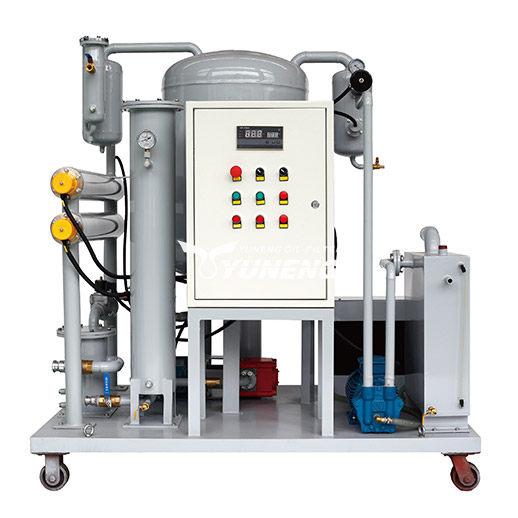
Working principle of hydraulic oil Filtration Machine
The operation of hydraulic oil filtration machines is based on a combination of three core principles: physical filtration, chemical adsorption, and heat treatment.
- Physical filtration: This main method utilizes filtering elements to remove solid pollutants from oil. These filtering elements are usually made of metal mesh, synthetic fibers, or ceramic materials, designed with specific pore sizes to capture particles exceeding a certain size. When the oil flows through the filter element, pollutants are trapped on its surface, while clean oil passes through. The selection of filter material and aperture depends on the required level of filtration accuracy to meet the specific requirements of hydraulic systems.
- Chemical adsorption: This process utilizes the strong adsorption properties of materials such as activated carbon to eliminate harmful substances in oil. Activated carbon has a highly porous structure and a huge network of microscopic cavities. These cavities act like magnets, attracting and capturing unwanted elements in oil, such as acidic compounds, oxidation products formed during oil degradation, and additives that have achieved their objectives. By adding an adsorption tower filled with activated carbon to the hydraulic oil filter, these harmful components in the oil can be effectively removed, thereby extending its service life and enhancing the health of the system.
- Heat treatment: In some applications, heat treatment is used to remove moisture and volatile substances from oil. This process involves using electric heating elements or steam heaters to heat the oil to a predetermined temperature. Heat promotes the evaporation of water and other volatile pollutants present in oil. In addition, heat treatment can accelerate certain chemical reactions within the oil, and improve its overall stability and antioxidant properties. However, maintaining precise control over heating temperature and duration is crucial to prevent oil degradation.
Structure of a Hydraulic Oil Filtration Machine
The hydraulic oil purifier is composed of multiple key components that work together to provide the best oil purification effect.
- Oil pump: This component acts as the driving force of the machine, responsible for extracting contaminated oil from the hydraulic system’s oil tank and guiding it to the filtration stage. The performance of the oil pump directly affects the overall efficiency and processing capacity of the hydraulic oil purifier.
- Heater: As mentioned earlier, the heater plays a crucial role in the heat treatment process. According to the selected heating method, the machine may include electric heating elements or steam heating systems. Accurate temperature control mechanisms are crucial for ensuring safe and effective oil heating.
- Filter cartridge: As the core of the physical filtration process, the filter cartridge is responsible for capturing solid pollutants in the oil. The selection of filter element materials and micron level is crucial for achieving the required level of filtration accuracy.
- Adsorption tower: This component accommodates the activated carbon medium used for chemical adsorption. The design and material selection of adsorption towers significantly affect their effectiveness in removing harmful substances from oil.
- Cooler: After filtration and in some cases, heat treatment, the oil needs to be cooled to an appropriate operating temperature range. The cooler usually uses water or air as the cooling medium to ensure that the processed oil returns to the hydraulic system at the optimal temperature.
- Auxiliary device: Hydraulic oil purifiers typically include additional monitoring and control functions to optimize their operation. These may include pressure gauges for monitoring oil pressure within the system, vacuum gauges for tracking pressure differences between filtering elements, and temperature sensors for maintaining precise control over heating and cooling processes.
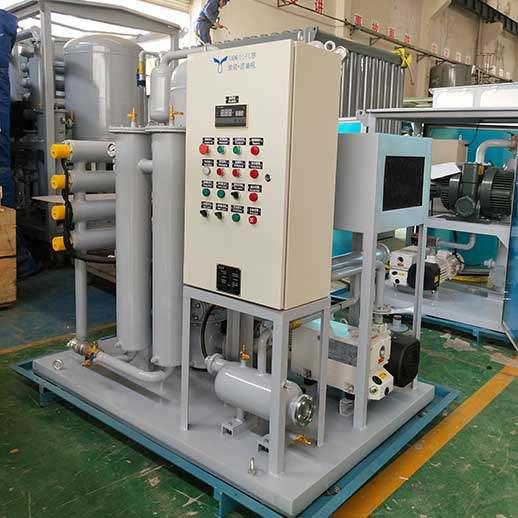
Multiple Applications of Hydraulic Oil Filtration Machines
Hydraulic oil filtration machines are widely used in various industries and play a crucial role in ensuring the smooth operation and service life of hydraulic systems. Here are some examples:
- Oilfield industry: In the harsh environment of oil exploration and production, the drilling fluid and mud used in drilling operations may be contaminated by various impurities. The hydraulic oil filtration machine ensures the cleanliness of these liquids, protects the integrity of drilling equipment, and optimizes drilling efficiency.
- Mining industry: Hydraulic systems are widely used in mining machinery to operate excavators, loaders, and other equipment. Hydraulic oil contamination in these machines may lead to malfunctions and costly shutdowns. Hydraulic oil purifiers play a crucial role in maintaining oil cleanliness by removing wear debris, dirt particles, and moisture, thereby minimizing equipment wear, preventing component failures, and extending maintenance intervals.
- Metallurgical industry: Hydraulic systems are crucial for the operation of steel mills and rolling equipment. The contamination of hydraulic oil during these processes may lead to malfunctions, disrupting production plans and potentially damaging expensive equipment. The hydraulic oil purifier ensures the cleanliness and quality of the hydraulic oil used in steelmaking and rolling processes, promotes smooth operation, minimizes downtime, and maintains equipment integrity.
- Power generation industry: Hydraulic systems play a crucial role in the control and regulation of equipment within power plants. The contamination of hydraulic oil in these systems can affect the efficiency and reliability of power generation. Hydraulic oil purifiers are used to maintain optimal oil quality, ensure the smooth operation of power plant equipment, and prevent potential faults that may interrupt power generation.
- Transportation industry: Mobile hydraulic systems are widely used in fields such as automobiles, construction machinery, and agricultural equipment. The hydraulic oil contamination in these vehicles can lead to performance degradation, increased component wear, and potential malfunctions. Hydraulic oil purifiers are used to maintain the cleanliness of hydraulic oil in mobile devices, ensuring optimal performance, extending equipment lifespan, and minimizing maintenance costs.
- Manufacturing industry: Hydraulic systems are widely used in manufacturing facilities for machine tools, robot systems, and hydraulic presses. Hydraulic oil contamination in these systems can lead to reduced accuracy, equipment failure, and decreased product quality. The hydraulic oil purifier is used to maintain the cleanliness of the hydraulic oil used in the manufacturing process, ensuring smooth operation, high accuracy, and stable product quality.
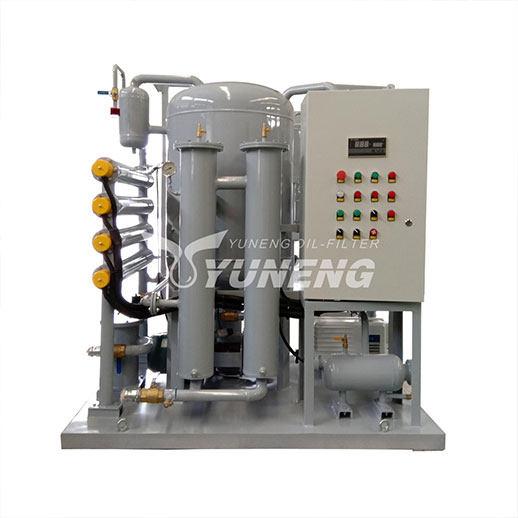
Considerations for Choosing the Right Hydraulic Oil Filtration Machine
- Filtering accuracy: The required level of filtering accuracy depends on the specific tolerances and cleanliness requirements of the hydraulic system. For systems that require excellent cleanliness, such as those in precision machining or medical equipment, achieving higher precision filtration through finer filtering elements is necessary.
- Flow characteristics: The flow rate of the hydraulic oil purifier needs to be sufficient to handle the oil flow in the hydraulic system. Choosing a machine with insufficient traffic may lead to bottlenecks and pressure drops within the system, thereby affecting its performance.
- Filter strength: The filter should have sufficient strength to withstand the working pressure in the hydraulic system. Fragile filtering elements may rupture under pressure, allowing pollutants to bypass the filter and potentially causing serious damage to the system.
- Installation space: The physical dimensions of the hydraulic oil purifier need to match the available space on the installation site. Portable filtering devices provide greater flexibility for situations with limited space.
- Maintenance cost: The selection process should consider the ongoing costs related to filter replacement and general maintenance of hydraulic oil purifiers. Machines with easily accessible filtering elements and user-friendly maintenance programs can minimize downtime and maintenance costs.
- After-sales service: Reliable after-sales service from manufacturers is crucial to ensure timely resolution of any technical issues that may arise during machine operation. A reputable manufacturer with a strong service network can provide you with peace of mind and minimize downtime in the event of unexpected problems.
- Environmental friendliness: With the increasing severity of environmental problems, the impact of hydraulic oil purifiers on the environment should be considered. Select machines that use environmentally friendly disposal methods to treat waste filtration components and minimize energy consumption during operation.
Regular Maintenance to Maintain Optimal Performance of Hydraulic Oil Filtration Machines
Regular and correct maintenance is crucial to ensure the optimal performance and service life of hydraulic oil filtration machines. Here are some key practices to follow:
- Regular inspection of the filter element: The filter element is the front line for preventing pollution, and its effectiveness will weaken with the capture of pollutants. Regular inspection of filter components (usually recommended every 2000 to 5000 operating hours) is crucial for identifying clogged or damaged components that need to be replaced. Timely replacement of used filter elements can ensure continuous and effective filtration and protect the hydraulic system from contamination.
- Tank cleaning: Over time, sludge and impurities will accumulate at the bottom of the hydraulic tank. Regular cleaning of the fuel tank (usually recommended every six months) helps prevent these pollutants from re-entering the oil during the filtration process. A clean fuel tank helps maintain the overall cleanliness of the oil and the health of the system.
- Oil pump and pipeline inspection: The oil pump and pipeline are important components responsible for oil circulation inside the filter. Regular inspection of these components for signs of wear, leakage, or damage is crucial. Early detection, repair, or replacement of worn or damaged oil pumps and pipelines can ensure the smooth operation of the filter and prevent potential oil leaks or malfunctions.
- Electrical system inspection: The electrical system controls various functions inside the hydraulic oil filtration machine. Regular inspection of electrical components for faults or loose connections is crucial. Timely troubleshooting and correction of any electrical issues can ensure reliable machine operation and prevent potential malfunctions.
- Maintenance Record Preservation: Maintaining a detailed record of all maintenance activities carried out on the hydraulic oil filter, including dates, types of maintenance performed, and replacement parts used, is very beneficial. These records provide valuable insights into the operating history of machines and help identify potential trends or issues that require attention. Regular review of maintenance records can enable proactive maintenance practices and help prevent unexpected downtime.
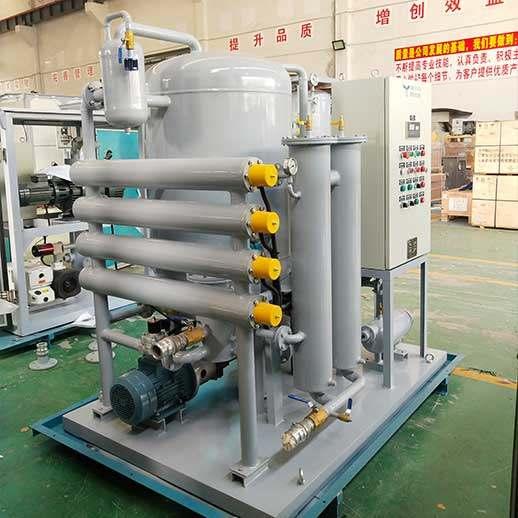
Troubleshooting Common Problems of Hydraulic Oil Filtration Machines
Despite proper maintenance, hydraulic oil filters occasionally run into problems. Here’s a breakdown of some common problems and potential solutions:
- Poor filtration: This can be caused by blocked filter elements, the reintroduction of impurities from a contaminated tank, or insufficient oil flow to the pump. Solutions include replacing clogged filter elements, cleaning the fuel tank, and checking the pump for wear or failure.
- Excessive equipment noise: Increased noise levels can indicate oil pump wear, leaks in pipes or connections, or blocked filter elements. Solutions include replacing worn pumps, fixing leaks, or replacing clogged filter elements.
- Equipment leaks: Leaks may occur due to loose pipe connections or damaged fuel tanks. Tightening loose connections or repairing/replacing the tank can repair leaks and prevent oil loss.
- Device failure to start: This may be due to a power failure or electrical system failure. To solve this problem, you must check the power supply and troubleshoot the electrical components.
By addressing these common issues in a timely manner, you can minimize downtime and ensure the continuous smooth operation of your hydraulic oil filter.
Conclusion
Hydraulic oil purifiers play a vital role in ensuring the health and performance of hydraulic systems in various industries. By understanding how they work, their construction, and their different applications, you can make informed decisions when choosing and maintaining these important machines. Regular maintenance and timely troubleshooting of any problems ensure optimal performance and extended service life of the hydraulic oil purifier and the hydraulic system it protects. Investing in a high-quality hydraulic oil filter and following proper maintenance practices is a cost-effective strategy to maximize the efficiency, reliability, and service life of hydraulic systems in industrial operations.