The Role of SF6 Gas Recycling and Filling Equipment in Sustainable Grid Operation
Sulfur hexafluoride (SF6) – a colorless, odorless, and surprisingly non-toxic gas – plays a crucial role in the modern world’s electrical grid. Its insulating and arc-suppressing properties make it a vital component in high-voltage equipment like transformers, circuit breakers, and gas-insulated switchgear (GIS). However, this very utility comes with a hidden cost: SF6 is a potent greenhouse gas, contributing to climate change if not managed responsibly. This stark reality places us at a crossroads – harnessing the benefits of SF6 while minimizing its environmental impact. The SF6 gas recycling and filling equipment – a technological marvel that allows us to reap the benefits of this gas while minimizing its environmental impact.
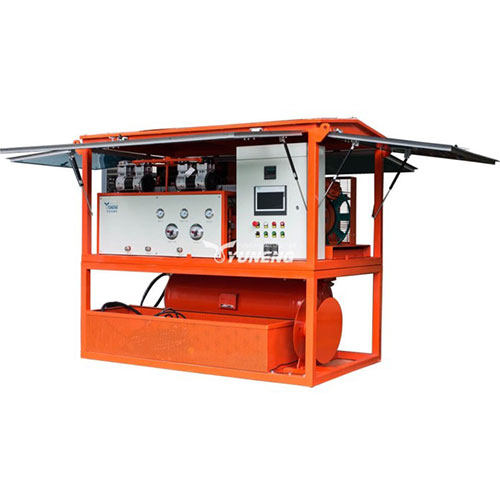
How Does SF6 Gas Recycling and Filling Equipment Work?
The operation of SF6 gas recycling and filling equipment involves several steps to ensure the proper handling and management of the gas. Here’s a general overview of how SF6 gas recycling and filling equipment typically works:
Stage 1: Isolation and Depressurization
- Circuit De-Energization: Prior to any physical isolation, the target equipment containing the spent SF6 is meticulously de-energized through established safety protocols to ensure operator safety and prevent electrical hazards.
- Pressure Isolation: Upon de-energization, the equipment is physically isolated from the operational power grid by employing multiple redundant isolation valve configurations. This ensures complete system isolation and the containment of spent SF6 within the designated circuit.
- Deep Vacuum Depressurization: A high-capacity rotary vane or two-stage piston vacuum pump initiates the extraction process by establishing a controlled negative pressure differential within the isolated equipment. This differential pressure “coaxes” the spent SF6 gas out of the equipment and into the recycling system’s intake manifold.
Stage 2: Multi-Stage Contaminant Removal
- Particulate Filtration: The extracted gas first encounters high-efficiency coalescing filters specifically designed to capture micron-sized solid contaminants like metallic oxides and dust particles. This safeguards downstream purification stages and ensures gas purity.
- Moisture Desorption: To prevent ice crystal formation and potential equipment damage, the gas is processed through a desiccating media bed or cryogenic chiller to remove water vapor. This process alters the gas dew point, ensuring moisture levels remain below critical condensation thresholds.
- Hydrocarbon Separation: Specialized oil separators or coalescing filters efficiently remove oil vapor and liquid hydrocarbons from the gas stream. This protects downstream components from potential oil contamination and preserves dielectric strength.
- Decomposition Product Scrubbing: Advanced adsorption beds or chemical scrubbing systems neutralize harmful decomposition byproducts like carbonyl fluoride and sulfur oxyfluoride. This restores the gas’s dielectric integrity and environmental safety.
Stage 3: Secure High-Pressure Storage
- Transfer and Compression: The revitalized SF6 gas is safely transferred through pressure-rated piping and compressed by dedicated compressors before storage. This increases gas density for efficient storage and facilitates future redeployment.
- High-Pressure Cylinder/Tank Containment: The compressed gas is securely stored in high-pressure cylinders or tanks specifically designed to withstand the unique thermal and pressure properties of SF6. These vessels comply with stringent safety regulations and ensure gas integrity until redeployment.
Stage 4: Precise Refilling and System Reintegration
- Pressure and Flow Rate Control: Upon redeployment, the purified SF6 gas is meticulously reintroduced into the target equipment using precision-controlled valves and metering devices. This ensures optimal flow rates and prevents overfilling, which can compromise equipment performance and safety.
- Vacuum Purge and System Re-Energization: Following a successful gas refill, a controlled vacuum purge removes any residual non-condensable gases from the equipment. Finally, the circuit is safely re-energized and integrated back into the operational power grid.
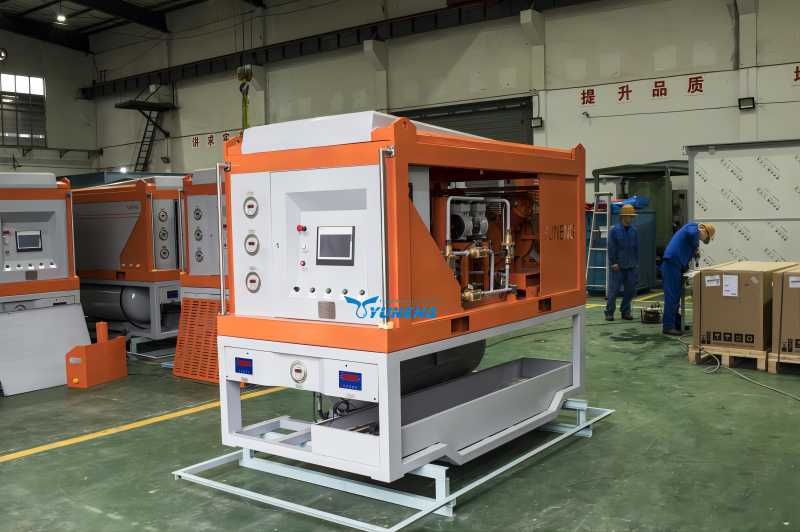
The Crucial Role of SF6 Gas Recycling and Filling Equipment in Electrical Grids
The versatility of SF6 gas recycling and filling equipment extends throughout the entire electrical grid value chain, from generation to distribution, offering critical benefits in each domain:
- Power Generation Facilities: Within transformers and switchgear, this technology guarantees optimal dielectric integrity and arc suppression, safeguarding vital components responsible for electricity generation and voltage level adjustment.
- Transmission and Distribution Substations: As the central hubs of power distribution, substations rely heavily on SF6-insulated equipment for reliable power transfer and voltage regulation. Recycling and refilling prolongs the operational life of this crucial infrastructure, minimizing replacement costs and ensuring uninterrupted service.
- Transmission Line Connections: Gas-insulated switchgear (GIS) leverages SF6’s insulating properties for compact and efficient transmission line connections. Recycling and refilling significantly reduce the environmental footprint and maintenance requirements of these vital grid arteries.
- Distribution Networks: Distribution transformers and switchgear utilize SF6 for safe and reliable power delivery to residential and commercial consumers. Recycling and refilling ensure consistent performance while minimizing environmental impact through reduced reliance on virgin SF6.
Compelling Reasons to Adopt SF6 Gas Recycling and Filling Equipment
The utilization of SF6 (Sulfur Hexafluoride) gas recycling and filling equipment is driven by several compelling reasons, reflecting a commitment to environmental sustainability, regulatory compliance, and the efficient management of high-voltage electrical systems. Here are key reasons why SF6 gas recycling and filling equipment are essential:
1. Environmental Imperative: Minimizing the Footprint
- Green Champion: By reducing the need for virgin SF6, a notorious climate culprit, this equipment significantly lowers greenhouse gas emissions. This translates to a smaller footprint on our planet and aligns with global efforts to combat climate change.
- Closed-Loop Aspiration: The future beckons with advancements in closed-loop systems that minimize emissions and maximize gas reuse. This vision of near-zero waste holds immense potential for further environmental benefit.
2. Economic Efficiency: Turning Waste into Savings
- Cost-Cutting Hero: Recycling and refilling dramatically reduces the reliance on expensive virgin SF6, bringing substantial cost savings to power companies. These savings ultimately ripple down to consumers in the form of lower electricity bills.
- Extended Equipment Life: By removing contaminants and preventing decomposition, this technology extends the lifespan of electrical equipment. This reduces the need for replacements and maintenance, contributing to further cost savings and resource conservation.
3. Operational Excellence: A Boost for Reliability and Safety
- Performance Enhancer: Contaminant-free SF6 gas boasts superior insulating and arc-suppressing properties. This translates to enhanced equipment performance, improved reliability of the grid, and minimized risk of power outages.
- Safety Guardian: Eliminating harmful byproducts from the gas stream fosters a safer working environment for personnel and minimizes the risk of electrical accidents within high-voltage equipment.
4. Technological Innovation
- Deep Vacuum Powerhouses: Robust vacuum pumps, the workhorses of the operation, extract spent gas using cutting-edge deep vacuum technology, initiating the recycling process.
- Multi-Stage Purification: A symphony of filtration, desiccation, oil separation, and decomposition scrubbing techniques meticulously remove contaminants, restoring the gas to its pristine state.
- Precision Refilling: Valves and metering devices, guided by intelligent control systems, meticulously reintroduce the purified gas into equipment at optimal pressure and flow rates, ensuring peak performance and preventing overfilling.
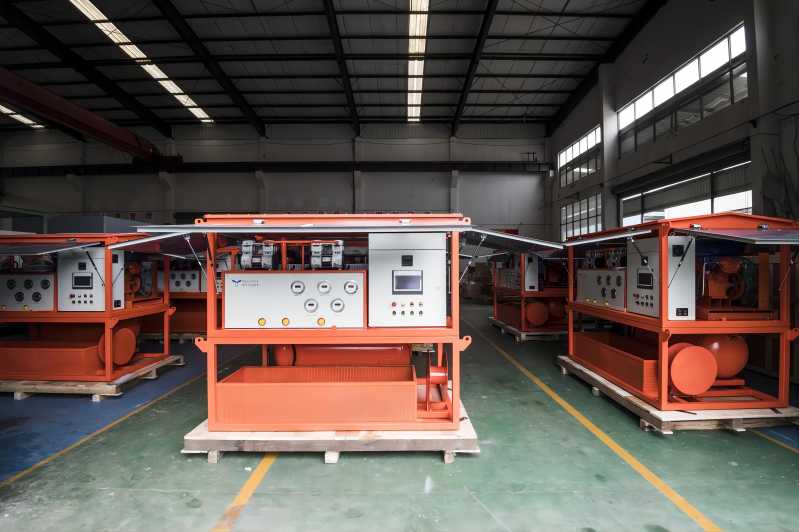
Regulations and Considerations of SF6 Gas Recycling and Filling Equipment
While SF6 gas recycling and filling equipment promises a greener future for the electrical grid, its operation is not without caveats. A complex web of regulations and considerations surrounds this technology, demanding careful navigation to ensure safe, efficient, and environmentally responsible practices. Here are some key regulations and considerations that govern the use of SF6 gas recycling and filling equipment:
1. Regulatory Framework
- International: The Kyoto Protocol and Kigali Amendment to the Montreal Protocol set overarching global frameworks for managing fluorinated greenhouse gases, including SF6. These agreements establish emission reduction targets and dictate responsible handling practices.
- Regional and National: Specific regulations on SF6 handling and equipment utilization vary by region and nation. Key areas covered include equipment certification, emission limits, waste management protocols, and reporting requirements. Consulting with relevant regulatory bodies within your jurisdiction is paramount for ensuring compliance.
- Industry Standards: Industry-specific standards and best practices, such as IEC 60480 for gas-insulated switchgear, provide additional guidance on equipment performance, maintenance, and operation. Adherence to these standards ensures alignment with industry norms and enhances operational safety and reliability.
2. Critical Considerations
- Equipment Selection: Choosing equipment that meets relevant regulations and industry standards is essential. Factors like gas compatibility, purification capabilities, and leakage rates should be carefully considered to ensure optimal performance and compliance.
- Operator Training: Proper training for personnel operating and maintaining the equipment is vital. This includes understanding safety protocols, emergency procedures, and proper gas handling techniques to ensure safe and efficient operation.
- Maintenance and Calibration: Regular maintenance and calibration of equipment are critical for ensuring accurate gas measurements, efficient purification, and continued compliance with regulations. Develop a robust maintenance schedule and adhere to manufacturer recommendations.
- Waste Management: Responsible disposal of waste gas and contaminated materials is crucial. Utilize authorized waste disposal facilities that comply with environmental regulations and minimize environmental impact.
- Recordkeeping and Reporting: Maintaining accurate records of gas usage, emissions, and equipment maintenance is essential for regulatory compliance and environmental transparency. Familiarize yourself with reporting requirements within your jurisdiction and submit reports accurately and on time.
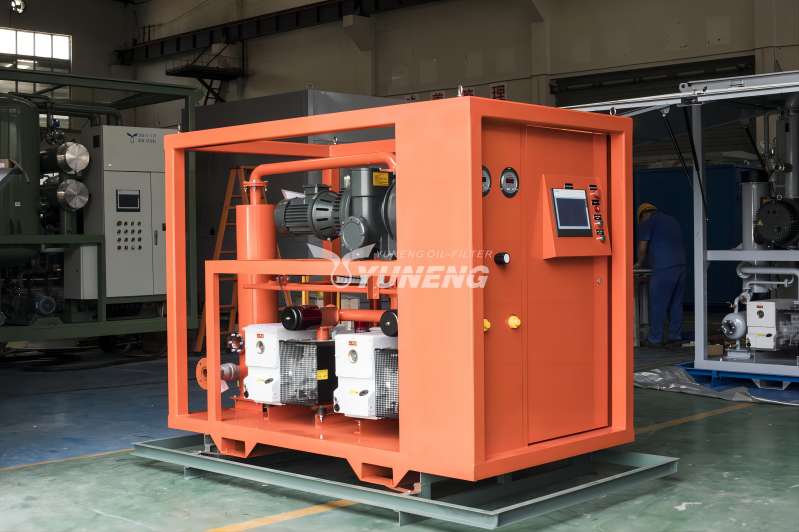
Conclusion
In conclusion, SF6 gas recycling and filling equipment presents a vital solution for the electrical grid, tackling the complex challenges of environmental responsibility and economic efficiency. From its ability to minimize greenhouse gas emissions and conserve resources to its cost-savings potential and enhanced equipment performance, this technology offers a comprehensive approach to sustainable grid operation. As we navigate the intricacies of regulations and best practices, continuous research and development pave the way for even greater advancements in efficiency and environmental benefit. By embracing this innovative technology and operating with dedication to responsible practices, we can ensure the continued flow of electricity for generations to come while safeguarding our planet for a brighter future.