What is Double Stage Vacuum Pumping for Transformers?
Vacuum pumping is a key link in transformer maintenance, which mainly includes two processes: vacuum pumping and oil filling. As a highly efficient vacuum equipment, the double-stage vacuum pump plays an important role in the transformer vacuum pumping and oil filling process. This equipment is usually used in many industries including power companies and substations, especially in large substations above 110KV for on-site transformer maintenance and deep treatment of new oil and imported oil.
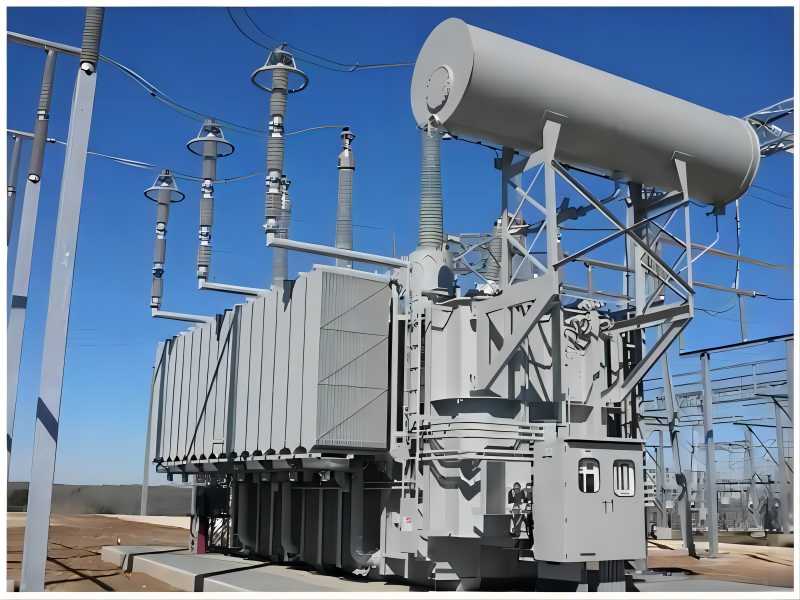
What is Double Stage Vacuum Pumping?
Double-stage vacuum pumping plays a central role in the manufacture of power transformers. By stripping away moisture, air, and stray contaminants, the method leaves the oil-filled chamber clean and ready for service, cutting the chance of electrical faults and giving the transformer a longer, healthier working life.
A roughing pump kicks off the operation by extracting most of the bulk gases and vapours, so the pressure inside drops into the low-vacuum range. Once that stage is finished, a high-vacuum pump takes over, reaching a far deeper vacuum and pursuing the stubborn traces that linger after the roughing step. Because some of those final impurities are heavier or stickier, the second pump is tuned to exhaust them even if their molecular size or chemistry resists.
Running the two pumps in tandem creates a level of vacuum that either one could miss on its own. The result is more than just a cleaner tank; the tighter evacuation reduces thermal losses once the transformer is in service and allows it to run cooler under load.
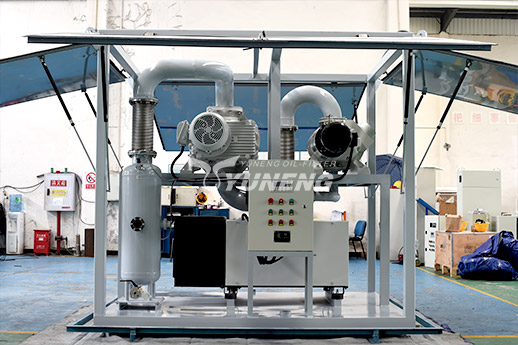
Double Stage Vacuum Pump in Transformer Vacuuming and Oil Filling Process
Two-stage vacuum pumps are standard equipment in the transformer yard, especially when the box needs both air removed and oil pushed in. The setup combines basic vacuum techniques with decent filtration and is quite straightforward once the jargon is set aside. We’ll discuss specifications and practical details a little later.
Application Principle in Transformer Vacuuming
The first and perhaps the most pressing job is getting all the air, what’s left of it after assembly, out of the tank. Oxygen, water vapour, and a handful of stray gases linger inside, none of which do the metal windings or the insulating oil any favours once power hits the circuit.
Moisture rusts components, oxygen promotes oxidation, and most insulating oils simply do not perform well under humid conditions. Reducing that humidity and oxygen level before the fill – or indeed before the first turn-on – avoids issues that most people never see, fortunately.
A two-stage design provides that double advantage by reducing pressure in two deliberate stages. The first ring of vanes removes the bulk of the air right off the top and lowers the absolute pressure to a lean pre-pump figure. Once that heavy lifting is done, the second stage kicks in like a fine adjustment, polishing away the last few molecules until the gauge reads near quiet space.
After that, a second-stage vacuum pump takes over, pursuing the last remnants of gas with its finer, more deliberate action. Because of that extra diligence, the transformers inside the cavity can achieve a noticeably tighter vacuum.
Running the two-stage setup in tandem, teams save minutes off the entire process while eliminating almost every trace of moisture and air from the tank. Achieving that emptiness ensures that the incoming oil has a clean, uninterrupted path as it fills the space.
Application Principle in Transformer Oil Filling
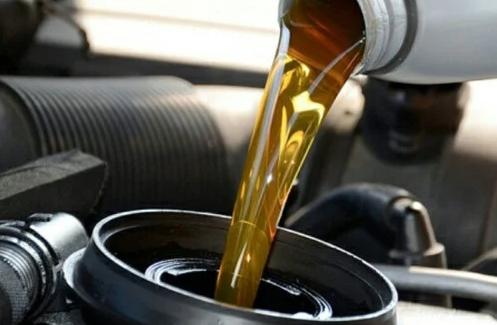
Insulating oil is deliberately pumped into a transformer until every cavity is filled and no air pockets can re-infiltrate. The oil functions both as a physical barrier and as the principal dielectric medium, preventing electrical discharge across insulated surfaces.
- A two-stage vacuum pump handles both evacuation and oil transfer in tandem. By holding the chamber under continuous vacuum while oil enters, the apparatus avoids the usual delay between these consecutive steps.
- That simultaneous strategy speeds the procedure considerably. The lowered pressure causes the fluid to flow briskly into narrow gaps so that all component surfaces receive a uniform coat almost instantly.
- Filling under vacuum also captures and removes microscopic bubbles that would otherwise linger in the oil. By denying any trace gas the chance to settle, the assembly achieves a more reliable dielectric strength once energised.
Vacuuming and oil-filling are conventionally performed as a single operation; their simultaneous execution undergirds both the immediate efficiency and the long-term reliability of the transformer. A high-performance, two-stage vacuum pump underwrites this pairing by generating and steadfastly holding the required low pressure, thus keeping the core internals flooded with oil and free of moisture throughout assembly and periodic servicing.
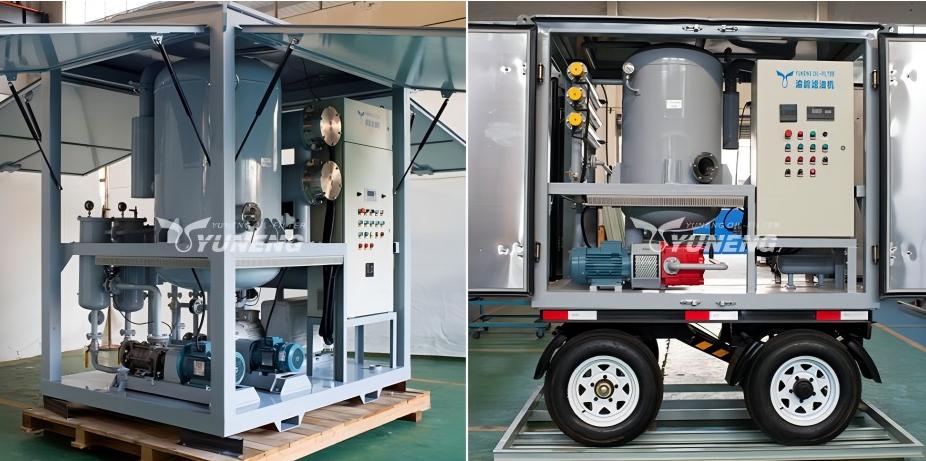
How Can You Benefit From Double Stage Vacuum Pumping?
Double-stage vacuum pumping has become a preferred technique among transformer manufacturers and maintenance crews for a number of practical reasons.
- The method elevates reliability by stripping away moisture and entrained gases; these contaminants otherwise compromise the dielectrics and invite electrical failures.
- Careful vacuuming, paired with meticulous oil filling, also extends a transformer’s working life, so operators face far fewer shutdowns and replacements.
- Equipment that receives that thorough treatment runs with less waste, meaning engineers observe energy losses diminish and operating budgets ease.
- Finally, adhering to this protocol helps firms tick the boxes of strict regulatory specifications, which boosts safety on the shop floor and in the field.
In summary, during the transformer vacuuming and oil filling process, the two-stage vacuum pump achieves efficient and safe treatment of transformer oil through its unique two-stage vacuum system and multi-stage filtration technology, combined with automatic control and safety protection functions. These technical features not only improve work efficiency but also ensure the operation quality and safety of the transformer.
With the continuous advancement of technology, the application of two-stage vacuum pumps in these fields will be more extensive and mature in the future.
If you are interested in other information about double stage vacuum pumping for transformers, or anything about transformer oil purify, YUNENG’ s service team will be happy to answer your questions.