A Guide to Transformer Oil Filtration Machines
Transformers are the workhorses of the power grid, playing a critical role in transmitting and distributing electricity efficiently. These crucial pieces of equipment rely on transformer oil, also known as insulating oil, for two primary functions: insulation and cooling. The oil acts as a non-conductive barrier between high-voltage windings, preventing electrical current from leaking, while simultaneously absorbing heat generated by the transformer’s operation.
However, transformer oil isn’t invincible. Over time, it undergoes degradation due to various factors like oxidation, moisture ingress, and dirt accumulation. This degradation compromises the oil’s insulating properties and heat transfer capabilities, ultimately leading to decreased transformer efficiency and increased risk of breakdowns. Here’s where transformer oil filtration machine comes into play.
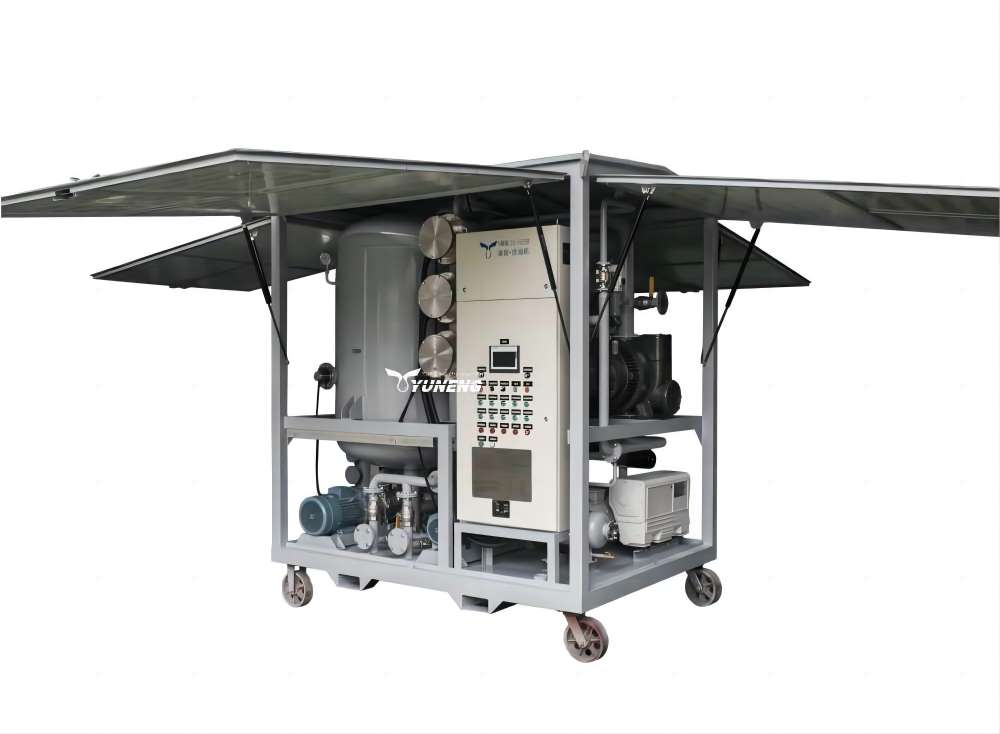
The Purpose of Transformer Oil Filtration
Transformer oil is subjected to a combination of stressors during operation. Oxygen exposure promotes oxidation, which breaks down oil molecules and generates harmful sludge and acids. Additionally, minute leaks or condensation can introduce moisture into the oil, further accelerating its degradation. Moisture contamination reduces the oil’s dielectric strength, increasing the risk of electrical breakdowns. Furthermore, airborne dust and dirt particles can also contaminate the oil, hindering its ability to effectively transfer heat.
The primary purpose of transformer oil filtration is to remove these contaminants and restore the oil’s original properties. By eliminating water, gas, and solid particles, filtration helps maintain the oil’s insulating strength, thermal conductivity, and overall health. This ensures efficient transformer operation, minimizes the risk of costly breakdowns, and extends the equipment’s lifespan.
Transformer Oil Filtration Machine Working Principle
Transformer oil filtration machines employ various technologies to remove contaminants and revitalize the oil’s properties. Here’s a detailed breakdown of two common methods:
1. Vacuum Dehydration
This method focuses on eliminating moisture (water) from the oil. Here’s a step-by-step explanation:
- Vacuum Pump Activation: The machine utilizes a vacuum pump to create a low-pressure environment within a sealed chamber.
- Reduced Boiling Point: Due to the lower pressure, the boiling point of water present in the transformer oil is significantly reduced. This makes it easier for the water to evaporate and separate from the oil.
- Evaporation and Removal: As the oil passes through the chamber, the lower pressure allows the water to readily transform from a liquid state to a vapor state. This vaporized water is then removed from the system by the vacuum pump.
- Filtration for Remaining Moisture: After the initial evaporation process, the oil is typically passed through a series of specialized filters. These filters capture any remaining moisture droplets or suspended water particles that may not have been eliminated in the initial stage. Additionally, these filters can also trap dissolved gases that may have been released from the oil during the vacuum process.
2. Fuller’s Earth Filtration
This method utilizes a specific type of filtration media to remove various contaminants from the oil. Here’s a breakdown of the process:
- Fuller’s Earth Clay: The core component of this method is a clay-based material called Fuller’s Earth. This clay has a specific property known as adsorption.
- Adsorption Process: Adsorption describes the phenomenon where molecules of a gas or liquid (contaminants in this case) become attached to the surface of a solid (Fuller’s earth clay in this case). During filtration, the oil is passed through canisters containing the Fuller’s earth media.
- Targeted Contaminant Removal: As the oil flows through the canisters, Fuller’s earth clay attracts and holds onto specific types of contaminants from the oil. These contaminants include polar molecules like water, acidic byproducts from oil degradation, and some other unwanted substances.
- Improved Oil Properties: By removing these contaminants, Fuller’s earth filtration helps improve the overall health of the transformer oil. Specifically, it can enhance the oil’s dielectric strength (resistance to electrical breakdown) and oxidation stability (resistance to oil breakdown due to oxygen exposure).
These are just two of the commonly used filtration technologies. Depending on the specific machine and the desired level of purification, additional filtration methods might be employed. However, the core principle remains the same across all methods: remove contaminants from the transformer oil to restore its original properties and ensure optimal transformer performance.
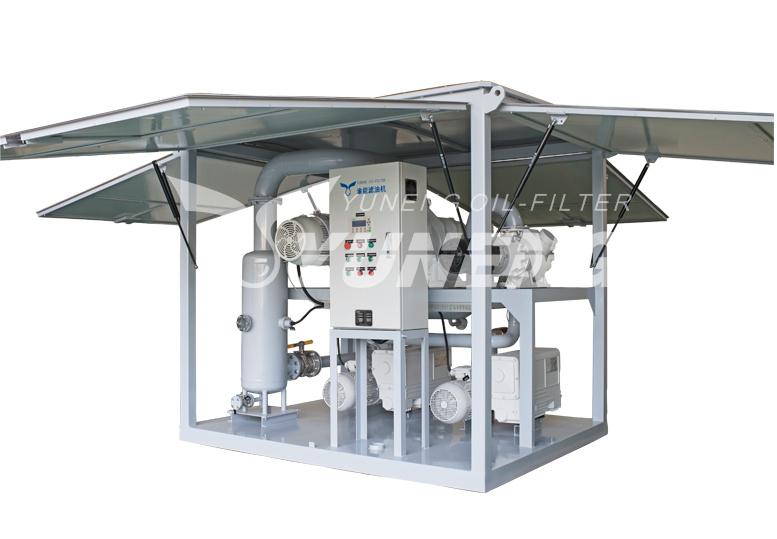
The Quality Standard of Transformer Oil Filtration
Transformer oil quality directly impacts the reliable and efficient operation of transformers in the power grid. To ensure optimal performance, industry standards established by organizations like ASTM International (American Society for Testing and Materials) provide specific guidelines for key oil properties. These standards define acceptable ranges for measurable parameters that directly influence the oil’s ability to function effectively as an insulator and coolant.
Here’s a breakdown of three critical parameters outlined in these standards:
- Breakdown Voltage (BDV): This parameter measures the oil’s electrical insulating strength. It reflects the voltage level at which the oil can withstand electrical current without experiencing a breakdown (arcing or sparking). A higher BDV indicates better insulating properties, crucial for preventing electrical faults within the transformer.
- Moisture Content: Excessive moisture contamination in transformer oil significantly reduces its dielectric strength (ability to resist electrical breakdown). Moisture can also accelerate the oil’s degradation process. Transformer oil standards specify a maximum allowable moisture content. Regular testing helps identify situations where moisture levels exceed acceptable limits, prompting the need for filtration.
- Interfacial Tension (IFT): This parameter reflects the cohesive forces within the oil molecules, impacting the oil’s ability to maintain a stable interface between itself and water. Proper IFT is crucial for preventing water from accumulating at the bottom of the transformer tank. If the oil-water interface weakens, water droplets can migrate and compromise the oil’s insulating properties. Regular testing of IFT helps ensure the oil maintains a strong interface, preventing water-related problems.
Regular transformer oil testing plays a vital role in monitoring these key parameters. When any of these parameters fall outside the acceptable ranges defined by industry standards, it’s a strong indicator that transformer oil filtration is necessary. Implementing proper filtration helps restore these parameters to within specified limits, ensuring the oil regains its effectiveness as an insulator and coolant, ultimately contributing to the reliable and efficient operation of the transformer.
Types of Transformer Oil Filtration Machines
Transformer oil filtration machines come in various types and designs, each tailored to specific requirements and capacities. Here are some common types:
- Vacuum Transformer Oil Filtration Machine: This type utilizes a vacuum process to remove moisture, gases, and impurities from transformer oil. It operates by creating a vacuum in the oil chamber, which helps in pulling out contaminants effectively.
- High-Efficiency Particulate Air (HEPA) Filtration Machine: HEPA filtration machines are designed to remove solid contaminants, such as dust, dirt, and metal particles, from transformer oil. They employ a series of filters, including HEPA filters, to achieve high filtration efficiency.
- Portable Transformer Oil Filtration Machine: These machines are compact and designed for easy transportation. They are suitable for on-site filtration of transformer oil, especially in locations where accessing the transformer is difficult.
- Stationary Transformer Oil Filtration Machine: Stationary filtration machines are larger and more powerful, suitable for industrial-scale applications where a high volume of transformer oil needs to be processed regularly.
- Regeneration Transformer Oil Filtration Machine: Regeneration machines not only filter the transformer oil but also regenerate it by removing aging by-products such as acids and sludge. They often use special adsorbent materials or chemical processes for regeneration.
- Online Transformer Oil Filtration System: Online filtration systems are designed to filter transformer oil while the transformer is in operation. They are integrated into the transformer’s oil circulation system and continuously filter the oil to maintain its cleanliness and dielectric strength.
- Degassing Transformer Oil Filtration Machine: These machines focus on removing dissolved gases, such as oxygen and nitrogen, from transformer oil. Degassing helps improve the insulating properties of the oil and extends the lifespan of the transformer.
- Mobile Transformer Oil Filtration Plant: Mobile plants are comprehensive filtration units mounted on trailers or trucks, offering mobility and flexibility in reaching different transformer sites for maintenance and filtration tasks.
- Dual Stage Transformer Oil Filtration Machine: Dual-stage filtration machines incorporate multiple filtration stages, often combining processes such as vacuum dehydration, particulate filtration, and degassing to achieve thorough purification of transformer oil.
- Automatic Transformer Oil Filtration System: These systems feature automated controls and sensors to monitor and regulate the filtration process, ensuring optimal efficiency and consistency without requiring constant manual intervention.
Choosing the right type of filtration machine depends on factors like the transformer size, oil contamination level, desired processing speed, and budget constraints. Consulting with a qualified transformer oil filtration service provider can help determine the most suitable machine for your specific needs.
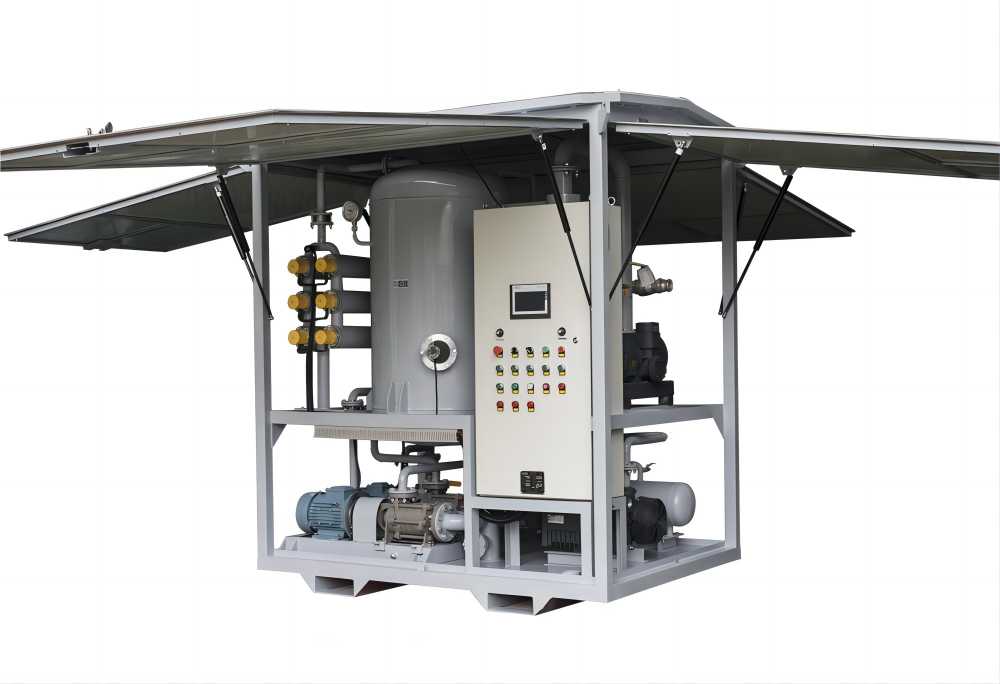
Tips for Choosing the Right Transformer Oil Purification Machine
Selecting the right transformer oil purification machine is crucial for achieving optimal results. Here are some key factors to consider:
- Transformer Size and Oil Capacity: The machine’s flow rate should be sufficient to process the oil volume within a reasonable timeframe. Larger transformers require machines with higher flow rates to ensure efficient oil circulation and filtration.
- Severity of Oil Contamination: The level of oil degradation determines the filtration method needed. Heavily contaminated oil might require a multi-stage filtration process or a machine with stronger contaminant removal capabilities. Conversely, mildly contaminated oil might be treatable with a simpler filtration system.
- Desired Features: Some transformer oil purification machines offer additional functionalities beyond basic filtration. These might include features like online filtration capability, which allows for oil processing while the transformer remains in operation. Other features could include built-in oil testing equipment or automated data logging for monitoring filtration progress and oil quality.
- Budget: Transformer oil filtration machines range in price depending on their size, capabilities, and brand. Consider the upfront cost of the machine balanced against the potential cost savings from extending transformer life and reducing the risk of breakdowns.
- Portability: If you require filtration for multiple transformers at different locations, a portable machine might be more suitable. However, for stationary use with a single transformer, a larger, offline machine might be more cost-effective.
- Vendor Reputation and Service: Choose a reputable vendor with a proven track record in transformer oil filtration solutions. Reliable after-sales service and readily available replacement parts are crucial for ensuring the long-term effectiveness of your chosen machine.
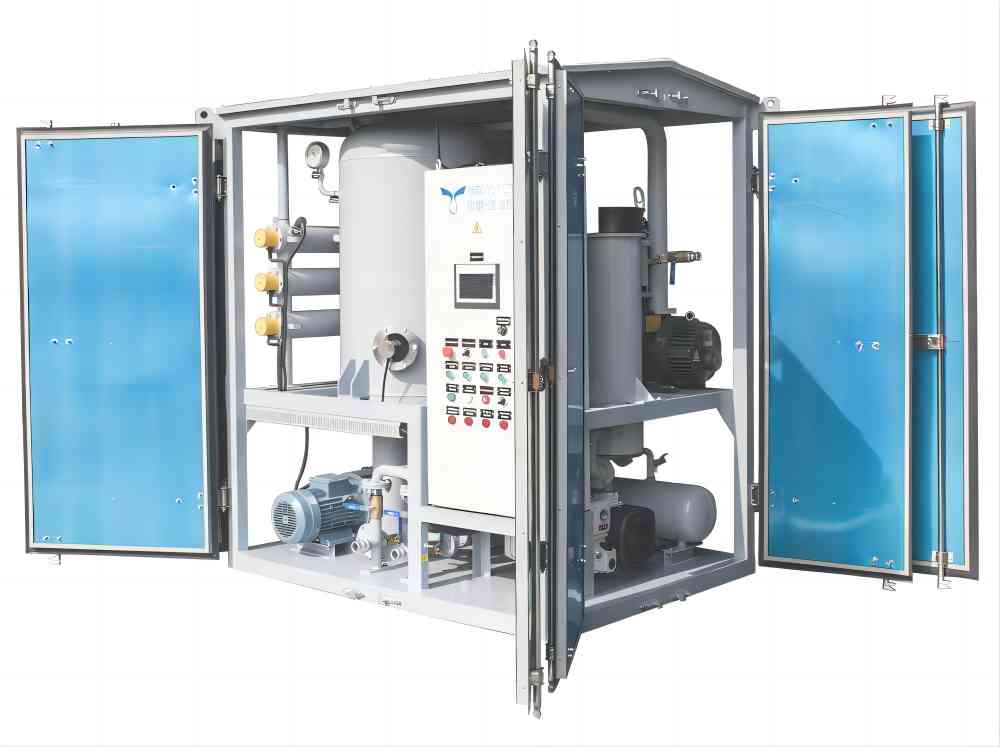
Conclusion
Transformer oil filtration plays a vital role in maintaining the health and performance of transformers. By removing contaminants and restoring the oil’s insulating and cooling properties, filtration helps ensure efficient power delivery while minimizing the risk of costly outages. Understanding the purpose and principles of transformer oil filtration empowers you to make informed decisions about selecting and implementing the most suitable solution for your specific needs. Regular oil filtration, combined with proper transformer maintenance practices, contributes significantly to extending transformer lifespan and ensuring reliable power for homes, businesses, and industries.