Foam Management in Vacuum Transformer Oil Purification Systems
Table of Contents
Transformer oil, a critical insulating and cooling medium in power transformers, is susceptible to degradation over time due to various factors, including contamination, oxidation, and thermal stress. To maintain its dielectric strength and operational efficiency, regular transformer oil purification is essential. However, the filtration process can introduce an undesirable phenomenon: foam formation. This article delves into the underlying causes of foam generation during transformer oil filtration, its detrimental effects on both the purification process and the transformer itself, and the comprehensive strategies to mitigate and prevent its occurrence.
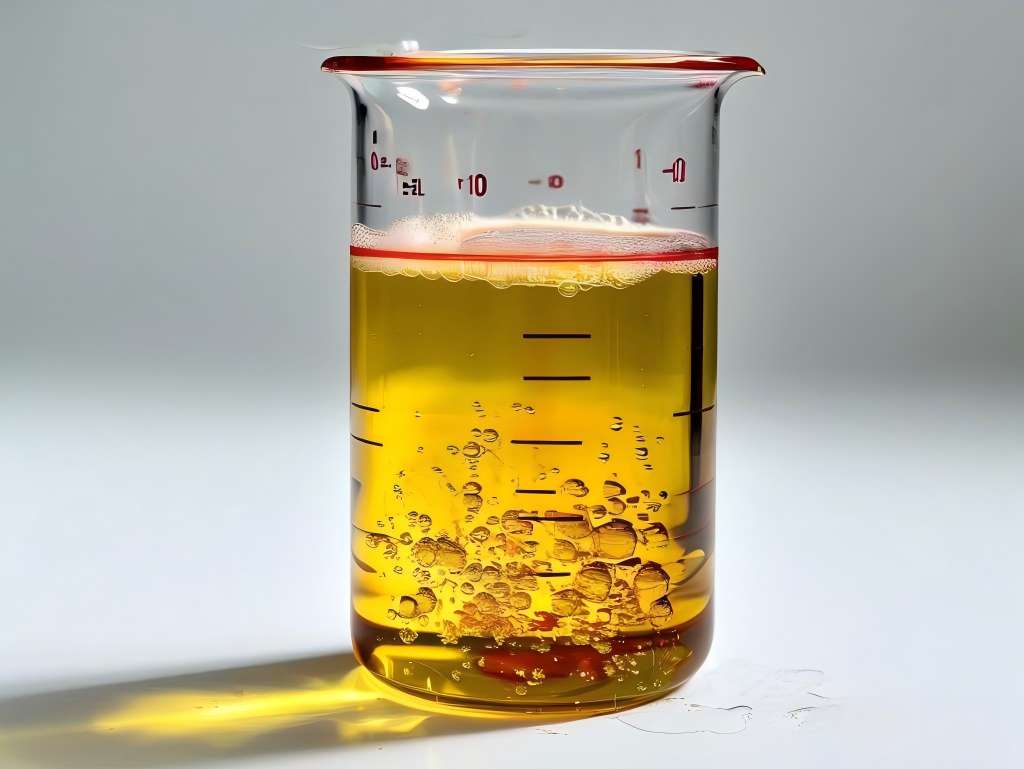
Causes of Foam Formation During Transformer Oil Purification
Foam formation in transformer oil during filtration is a complex phenomenon stemming from a synergistic interaction of factors related to the oil’s intrinsic properties, contaminants, additives, and the filtration process itself. Understanding these causes is crucial for implementing effective mitigation strategies.
1. Contaminants in the Oil
Moisture:
Water, even in trace amounts, significantly reduces the oil’s surface tension. This decrease in surface tension weakens the cohesive forces between oil molecules, making it easier for air or other gases to form stable bubbles, leading to foam. Water can exist in dissolved, emulsified, or free forms. During filtration, especially under vacuum conditions, dissolved and emulsified water can vaporize, contributing to foam.
Gases:
Transformer oil naturally contains dissolved gases, including air, nitrogen, and carbon dioxide. These gases remain dissolved under normal operating pressures. However, during filtration, particularly in vacuum oil purification systems or when subjected to pressure drops, the solubility of these gases decreases. This causes them to come out of solution, forming bubbles that contribute to foam. The amount of dissolved gas and the rate of its release are directly influenced by the temperature and pressure variations during the filtration process.
Solid Particles:
Particulate matter, such as dust, fibers, metallic debris, and carbon particles, acts as nucleation sites for bubble formation. These particles provide surfaces where gas bubbles can readily form and stabilize. The presence of solid particles also increases the oil’s viscosity and reduces its surface tension, further promoting foam stability.
Oil Degradation Products:
Oil oxidation and thermal decomposition produce various byproducts, including acids, sludge, and other polar compounds. These degradation products act as surfactants, reducing the oil’s surface tension and stabilizing foam. Sludge, in particular, increases the oil’s viscosity, making the foam more stable. Degradation products can also increase the amount of particulate matter in the oil.
2. Additives in the Oil
While additives like antioxidants (e.g., DBPC, BHT) and corrosion inhibitors are essential for prolonging oil life and enhancing performance, they can inadvertently contribute to foam formation.
Some additives, especially when present in high concentrations or when degraded, can alter the oil’s surface tension and foaming characteristics. Furthermore, the effectiveness of anti-foaming additives can diminish over time due to degradation or depletion. Additionally, the filter medium itself may remove some of the anti-foaming additive, rendering it ineffective.
3. Operational Factors During Filtration
- High Filtration Velocity: Rapid oil flow creates turbulence, leading to the entrainment of air and other gases into the oil. This turbulence increases the contact area between the oil and air, promoting the formation of small, stable bubbles that contribute to foam.
- Inadequate Equipment Sealing: Leaks in the filtration system, particularly around pumps, valves, and filter housings, allow air to enter the oil. This air ingress significantly increases the amount of dissolved gas in the oil, leading to excessive foam formation.
- Pressure Fluctuations: Sudden changes in pressure, especially in vacuum systems, cause dissolved gases to rapidly come out of solution. These rapid gas releases lead to the formation of large volumes of foam, which can disrupt the filtration process.
4. Oil Properties
- Surface Tension: Oils with low surface tension are inherently more susceptible to foam formation. The weaker intermolecular forces in these oils allow bubbles to form more easily and remain stable.
- Viscosity: Low-viscosity oils tend to generate more foam than high-viscosity oils. High-viscosity oils dampen the creation of bubbles and make the bubbles that are created less likely to remain stable. However, very high viscosity oils can stabilize foam if degradation products are present.
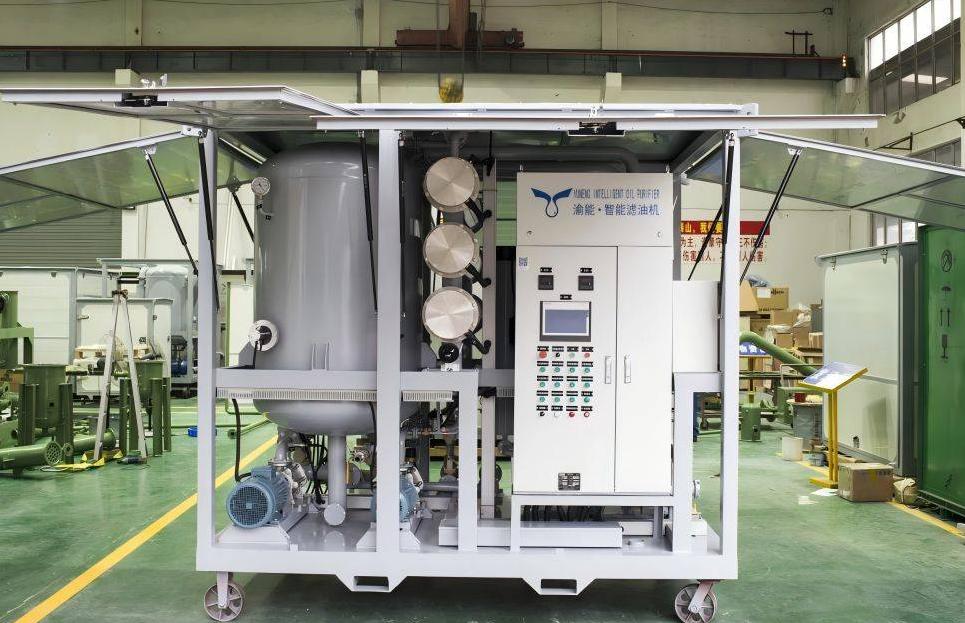
What are the Detrimental Impacts of Foam on Transformer Oil Purification and Transformer Operations?
The presence of foam during transformer oil filtration introduces a cascade of adverse effects, compromising both the efficiency of the purification process and the long-term reliability of the transformer itself. These impacts manifest as operational inefficiencies, heightened equipment stress, and a significant reduction in the transformer’s dielectric and thermal performance.
1. Impact on Transformer Oil Filtration Efficiency and Accuracy
Substantial Reduction in Filtration Efficiency:
Foam, by its very nature, introduces a significant increase in the volume of the fluid being processed. This increased volume, composed of gas bubbles interspersed within the oil, obstructs the flow of oil through the filter media. The result is a substantial reduction in the filtration rate, leading to prolonged processing times and increased energy consumption.
The foam also creates uneven flow patterns, causing filter media bypass and reducing the effectiveness of particulate removal.
Heightened Equipment Strain and Potential Damage:
The buildup of foam within the transformer oil filtration system creates an increased pressure drop across the filter elements. This elevated pressure places undue stress on pumps, valves, and other components, leading to premature wear and potential equipment failure.
The extra stress applied to the transformer oil filtration system can damage seals and other parts of the filter, leading to leaks and the entry of more air into the system, which will cause more foam.
Compromised Accuracy of Oil Quality Assessment:
The presence of foam significantly interferes with the accurate measurement of crucial oil quality parameters. For instance, moisture content readings can be skewed due to the presence of air bubbles, and dielectric strength measurements can be unreliable due to the distortion of electrical fields by the foam.
The bubbles within the foam can also interfere with the optical measurement methods that are used to determine the quality of the oil.
2. Impact on Transformer Operations and Longevity
Diminished Dielectric Strength and Increased Partial Discharge Risk:
Foam significantly reduces the oil’s dielectric strength, the ability of the oil to withstand electrical stress. This reduction increases the probability of partial discharges, which are localized electrical breakdowns within the insulation system.
The gaseous bubbles within the foam act as weak points in the insulation, providing pathways for electrical discharges. These discharges can progressively degrade the insulation, leading to catastrophic transformer failure.
Impaired Cooling Efficiency and Thermal Overstress:
Foam acts as a thermal insulator, hindering the efficient transfer of heat from the transformer windings to the surrounding oil. This results in localized hotspots and an overall increase in transformer operating temperature.
Elevated temperatures accelerate the degradation of both the oil and the solid insulation, shortening the transformer’s lifespan and increasing the risk of thermal failure.
Accelerated Oil Oxidation and Degradation:
The increased surface area created by foam promotes the oxidation of the transformer oil. This oxidation process leads to the formation of acids, sludge, and other degradation products, further compromising the oil’s insulating and cooling properties. The increased presence of oxygen, caused by the foam, increases the rate of oil degradation.
Elevated Risk of Catastrophic Transformer Failure:
The combination of reduced dielectric strength, impaired cooling, and accelerated oil degradation significantly increases the risk of catastrophic transformer failure. This can result in costly repairs, extended downtime, and potential safety hazards.
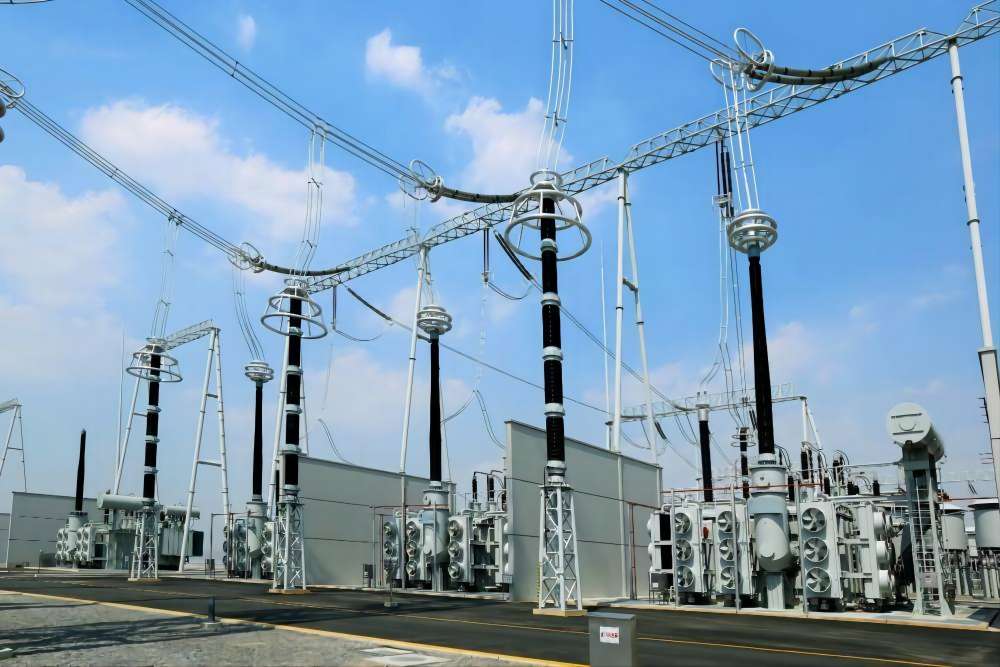
Strategies for Foam Mitigation During Transformer Oil Purification
To effectively combat foam formation and ensure optimal transformer oil purification, a holistic approach is required, integrating advanced equipment utilization, stringent oil quality control, and meticulous procedural refinements.
1. Optimization of Filtration Equipment and Processes for Enhanced Foam Control
Strategic Deployment of Vacuum Transformer Oil Purifiers:
The use of a high-efficiency vacuum transformer oil purifier is paramount. These systems excel at removing dissolved gases and moisture, the primary culprits behind foam formation.
The vacuum process significantly lowers the oil’s vapor pressure, facilitating the rapid release of dissolved gases and the evaporation of moisture. This robust degassing mechanism effectively minimizes foam generation. Vacuum oil purifiers also remove particulate matter, which acts as a nucleation point for foam.
Precision Control of Filtration Velocity:
Maintaining a carefully calibrated and consistent oil flow rate is crucial. Excessive flow rates induce turbulence, leading to air entrainment and the formation of persistent foam.
Employing variable-speed pumps and flow control valves enables precise regulation of oil velocity, minimizing turbulence and ensuring smooth, foam-free filtration.
Rigorous Equipment Sealing and Integrity Checks:
Ensuring airtight connections throughout the filtration system is essential. Regular inspections and maintenance of seals, gaskets, and connections prevent air ingress, a major contributor to foam formation.
Pressure testing the system after maintenance or component replacement can verify the integrity of the seals and prevent leaks.
Effective Oil Pretreatment for Heavily Contaminated Oils:
For oils with high levels of contaminants, implementing pretreatment methods, such as gravity settling or heating, can significantly reduce the load on the filtration system.
Settling allows heavy particulate matter to precipitate, while heating reduces oil viscosity, facilitating the release of dissolved gases and moisture before filtration.
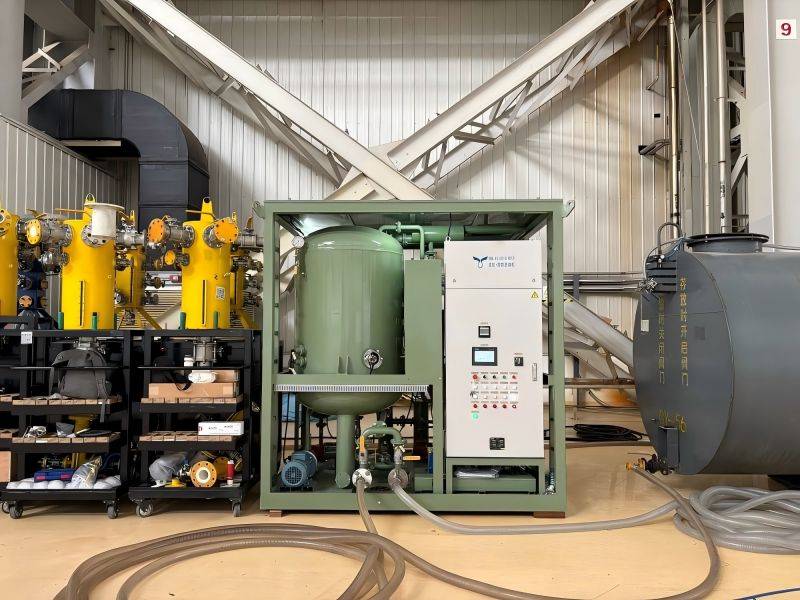
2. Stringent Oil Quality Control for Foam Prevention
Selection of Premium-Grade Transformer Oil:
Utilizing transformer oils that adhere to stringent purity and performance specifications minimizes the risk of foam formation.
Selecting oils with low surface tension and high resistance to oxidation ensures optimal performance and reduces the likelihood of foam-related issues.
Proactive Oil Testing and Preventive Maintenance:
Implementing a comprehensive transformer oil testing program, including regular analysis of moisture content, gas content, and particulate contamination, enables early detection of potential foam-inducing factors.
Regular oil replacement or regeneration, based on test results, helps maintain oil quality and prevent the accumulation of contaminants that contribute to foam.
Judicious Application of Compatible Antifoam Additives:
In situations where foam formation is persistent, the controlled addition of compatible antifoam additives can be effective.
It is crucial to select additives that are compatible with the transformer oil and do not compromise its dielectric or thermal properties. And to make sure that the filter medium does not remove the additive.
3. Refined Operational Procedures for Foam Minimization
Controlled and Gradual Oil Introduction:
Introducing oil into the filtration system in a controlled and gradual manner minimizes turbulence and air entrainment. Using slow-start pumps and controlled valve operation prevents sudden pressure surges that can lead to foam formation.
Precise Temperature Regulation:
Maintaining optimal oil temperature during transformer oil filtration is critical. Temperature influences gas solubility and oil viscosity, both of which affect foam formation. Employing temperature control systems ensures consistent oil temperature, minimizing gas evolution, and foam stability.
Implementation of Proper Grounding Practices:
Grounding the transformer oil filtration machine effectively minimizes the buildup of static electrical charges, which can contribute to the formation and stabilization of foam. Proper grounding also protects equipment and personnel from electrical hazards.
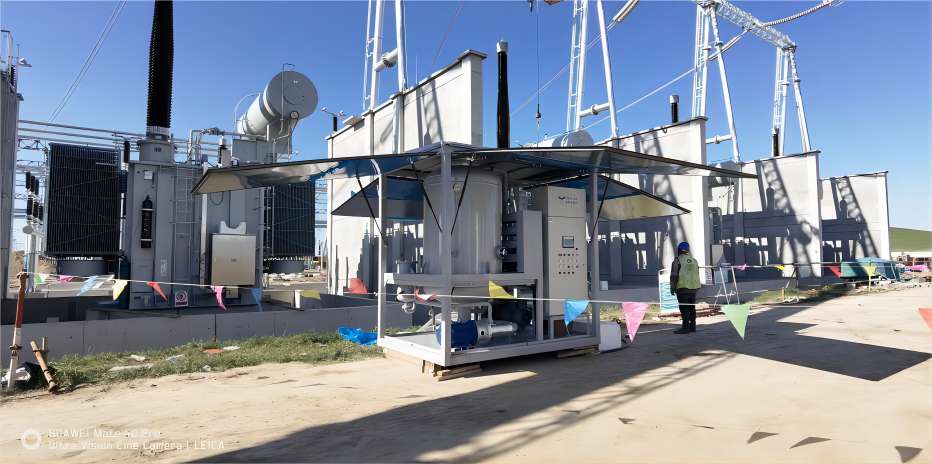
In Summary
Foam formation during transformer oil purification is a complex issue that requires a comprehensive understanding of its causes and impacts. By implementing the mitigation strategies outlined in this article, operators can ensure efficient and reliable oil purification, safeguarding the integrity and longevity of power transformers. The use of a vacuum transformer oil purifier is one of the most effective ways to remove dissolved gases and moisture, which are the main causes of foam. Continuous research and development in oil purification technologies will further enhance our ability to prevent and manage foam-related challenges, contributing to the reliable and sustainable operation of electrical power systems.