Intelligence and Automation in Transformer Oil Filtration: What Benefits Can Be Gained
Table of Contents
Transformer oil stands as the lifeblood of power transformers, fulfilling critical roles in electrical insulation, heat dissipation, and arc quenching. Maintaining its quality is paramount to the reliable and efficient operation of these vital assets within the power grid. Over time, transformer oil degrades due to thermal stress, oxidation, moisture ingress, and particulate contamination, compromising its dielectric strength and overall performance. Traditionally, transformer oil filtration has relied heavily on manual processes and periodic interventions. However, intelligentization and automation are ushering in a new era of transformer oil management, promising enhanced efficiency, reduced operational costs, and improved safety protocols.
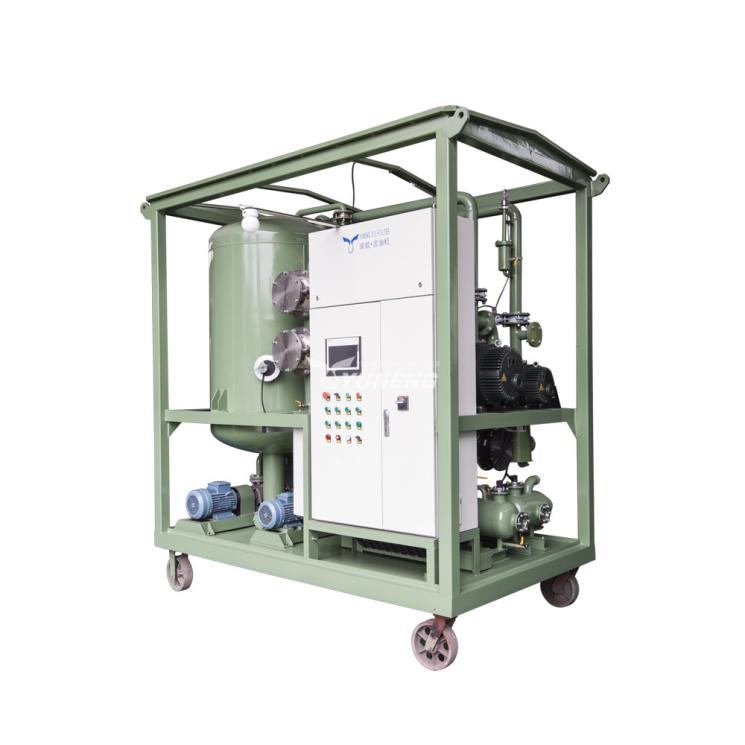
Why is Intelligent and Automated Filtration Important?
Conventional transformer oil filtration methods often present several limitations. They can be labor-intensive, requiring skilled personnel for setup, monitoring, and analysis. The intermittent nature of offline filtration may not provide a continuous understanding of the oil’s condition, potentially leading to delayed interventions and increased risks. Furthermore, manual sampling and laboratory analysis can be time-consuming, hindering proactive maintenance strategies.
The integration of intelligentization and automation directly addresses these shortcomings. By embedding sensors, data analytics, and automated control systems into filtration machines, a paradigm shift occurs from reactive maintenance to proactive and even predictive oil management. This evolution not only optimizes the filtration process itself but also provides valuable insights into the health of the transformer, contributing to the overall reliability and longevity of the power grid.
Key Applications of Intelligentization and Automation in Transformer Oil Filtration Machines
The intelligentization and automation of transformer oil filtration machines manifest in several key applications:
1. Real-time Oil Quality Monitoring and Intelligent Analysis
This cornerstone of the intelligent system involves the integration of an array of high-precision sensors capable of continuously measuring critical oil parameters. These sensors monitor moisture content, dissolved gas analysis (DGA) and particulate contamination levels. The data acquired by these sensors is then transmitted in real-time via Industrial Internet of Things (IIoT) protocols to cloud-based platforms or local monitoring systems.
Sophisticated algorithms, leveraging big data analytics and artificial intelligence (AI), analyze this continuous stream of data. Trend analysis algorithms can identify gradual degradation patterns, enabling early detection of potential issues. Diagnostic AI models can pinpoint the root causes of oil deterioration, such as overheating or internal faults within the transformer. Furthermore, predictive algorithms can forecast the remaining useful life of the oil and even predict potential equipment failures based on evolving oil conditions. The system can automatically generate comprehensive oil analysis reports and disseminate them to maintenance personnel via mobile applications or email notifications, facilitating timely and informed decision-making.
2. Automated Control of the Filtration Process
Intelligent transformer oil purifiers can autonomously manage the entire filtration cycle based on real-time oil quality data or pre-defined schedules. The system can automatically initiate the filtration process when oil quality parameters deviate from acceptable thresholds and cease operation once the desired standards are met. Flow rate and pressure are dynamically adjusted based on the oil’s viscosity and the concentration of contaminants, optimizing filtration efficiency.
The system also incorporates intelligent filter element monitoring, tracking pressure differentials, or accumulated contaminant levels. When a filter element becomes clogged or reaches its lifespan, the system automatically triggers alarms, prompting timely replacement. Integrated fault detection systems can identify anomalies such as motor overload, pump malfunctions, or abnormal oil levels, automatically initiating safety shutdowns and issuing alerts.
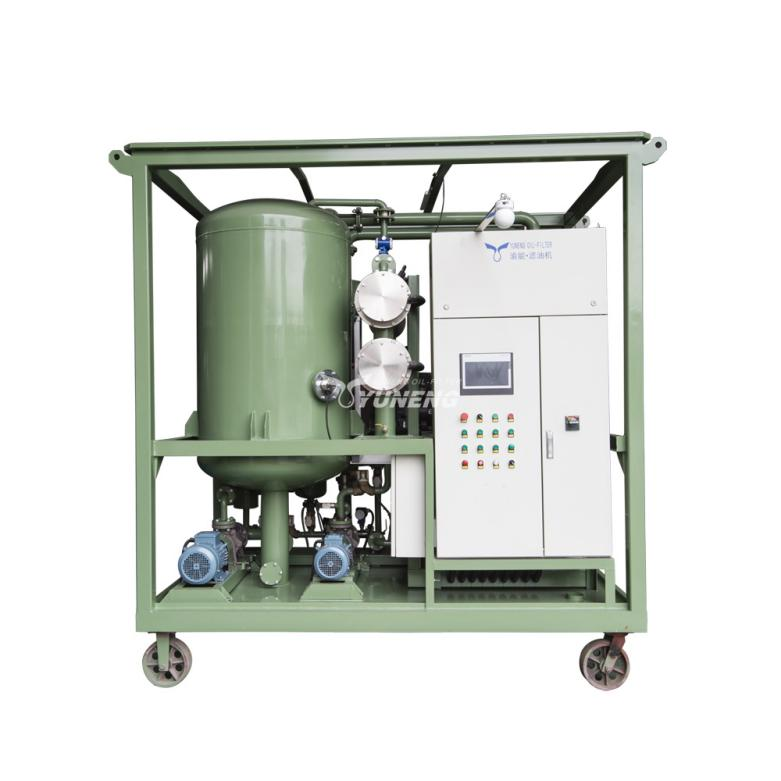
3. Remote Monitoring and Management
The connectivity afforded by IIoT enables remote oversight of the filtration process. Maintenance teams can access real-time operational status, oil quality data, and alarm logs from any location via computers or mobile devices. This remote access facilitates efficient monitoring and reduces the need for on-site inspections. Furthermore, authorized personnel can remotely configure operating parameters, adjust alarm thresholds, and even initiate or terminate filtration cycles.
In more advanced implementations, remote diagnostic capabilities allow experts to analyze historical data and current conditions remotely, providing accurate troubleshooting guidance and support. Integrating the filtration machine’s data into a broader plant-wide monitoring system offers a holistic view of asset health and operational performance.

4. Example of Yuneng ZJA Series Intelligent Transformer Oil Filtration Machine
The Yuneng ZJA series typically incorporates a comprehensive suite of online monitoring sensors, providing real-time data on key oil parameters such as moisture content, dissolved gas levels, dielectric strength, and particulate contamination. This continuous data acquisition forms the foundation for its intelligent operation. The integrated control system, often based on a PLC, automates the entire filtration process based on pre-set parameters or dynamically adjusts operation based on the real-time sensor readings.
Key intelligent features of the Yuneng ZJA series may include:
- Online Oil Quality Monitoring System: Integrated with high-precision sensors for real-time monitoring of key parameters such as moisture content, temperature, vacuum degree, and potentially dielectric strength and particle count (depending on the specific model).
- Intelligent Automatic Operation: PLC-based control system enables fully automatic operation, including automatic start/stop based on pre-set parameters or online sensor readings.
- Adaptive Filtration Control: The system can automatically adjust filtration parameters like flow rate and vacuum level based on the oil’s condition and contamination levels to optimize efficiency.
- Automatic Moisture and Degassing Control: Intelligent algorithms manage the vacuum degassing process to efficiently remove dissolved gases and moisture, with automatic adjustment of vacuum and temperature.
- Intelligent Filter Element Monitoring and Alarm: Real-time monitoring of filter element pressure differential with automatic alarms indicating the need for replacement.
- Safety Interlock System: Comprehensive safety features, including automatic shutdown in case of over-pressure, oil leakage, or motor overload, ensuring safe operation.
- Remote Monitoring and Control Interface: Equipped with interfaces for remote monitoring and control via computer or mobile devices, allowing for convenient operation and data access.
- Data Logging and Reporting: Automatic logging of operational data and oil quality parameters, with the ability to generate reports for analysis and record-keeping.
- Self-Diagnostic Capabilities: The system can perform self-diagnostics and provide error codes for easy troubleshooting.
- Optional DGA Online Monitoring Integration: Certain models can be integrated with online Dissolved Gas Analysis systems for a more comprehensive understanding of the transformer’s internal condition.
The Yuneng ZJA series highlights how intelligent automation can significantly enhance the efficiency and effectiveness of transformer oil filtration. By integrating online monitoring, automated control, and remote management capabilities, these machines reduce the need for manual intervention, provide real-time insights into oil condition, and contribute to a more proactive and reliable approach to transformer maintenance.
Underlying Technologies Enabling Intelligentization and Automation
The realization of intelligent and automated transformer oil filtration relies on several key technological advancements:
- High-Precision Sensor Technology: Accurate and reliable measurement of various oil parameters is fundamental. Advancements in chemical, physical, and electrical sensors provide the necessary precision and durability for continuous monitoring in harsh industrial environments.
- Industrial Internet of Things (IIoT) Technology: Robust and secure communication protocols and infrastructure are essential for seamless data acquisition, transmission, and remote control of the filtration equipment.
- Programmable Logic Controllers (PLCs) and Industrial Control Systems (ICS): These robust control systems form the brain of the automated filtration machine, executing control logic, managing actuators, and ensuring safe and efficient operation.
- Big Data Analytics and Artificial Intelligence (AI) Algorithms: Sophisticated algorithms are crucial for extracting meaningful insights from the vast amounts of data generated by the sensors, enabling predictive maintenance and proactive decision-making.
- Human-Machine Interface (HMI) and Mobile Application Development: User-friendly interfaces and mobile applications provide intuitive access to system data, control functions, and alerts, empowering maintenance personnel with the information they need.
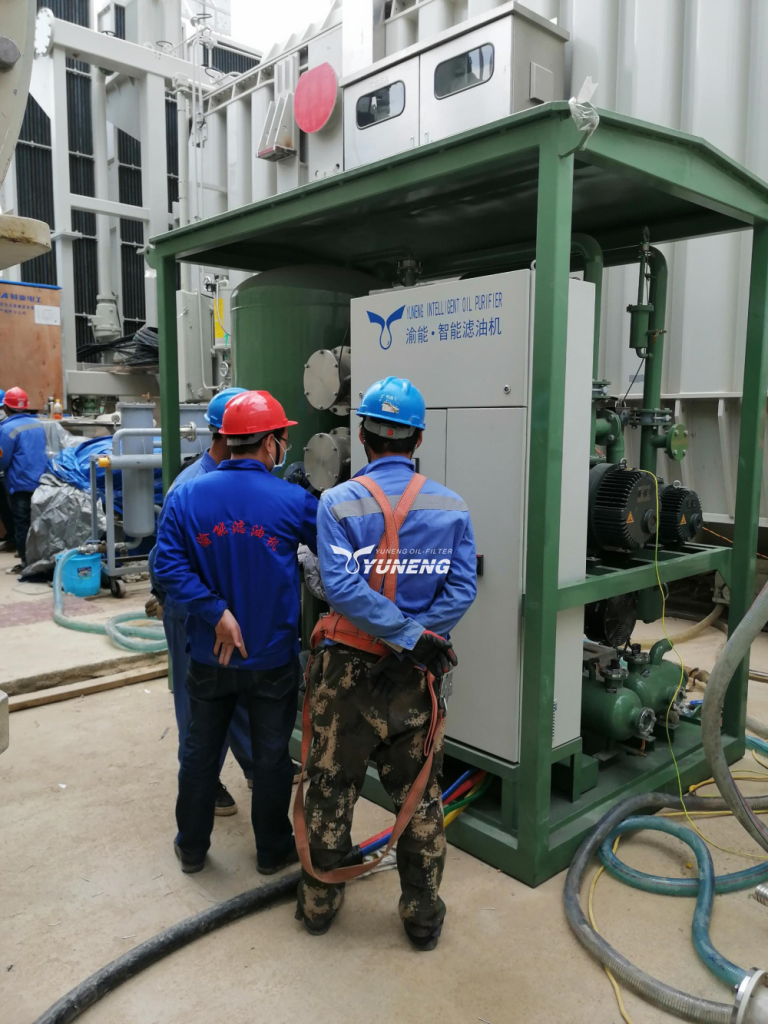
The Multifaceted Benefits of Intelligentization and Automation in Transformer Oil Filtration
The adoption of intelligent and automated transformer oil filtration machines yields a multitude of benefits:
- Enhanced Filtration Efficiency and Quality: Intelligent control ensures that filtration is performed optimally based on the actual condition of the oil, leading to more effective removal of contaminants and improved oil quality.
- Reduced Labor Costs: Automation minimizes the need for manual intervention, freeing up maintenance personnel for other critical tasks and reducing overall operational expenses.
- Extended Equipment and Oil Lifespan: Proactive oil management, enabled by continuous monitoring and timely filtration, mitigates oil degradation and reduces wear and tear on the transformer, extending the lifespan of both the oil and the equipment.
- Improved Operational Safety: Automated systems reduce the risk of human error during operation and maintenance, while early fault detection and automated safety shutdowns enhance overall safety protocols.
- Realization of Predictive Maintenance: By analyzing trends in oil quality data, potential issues can be identified and addressed proactively, minimizing unplanned downtime and maximizing asset availability.
- Elevated Management Level: Remote monitoring and centralized data management provide a comprehensive overview of the filtration process and transformer oil health, enabling more informed and efficient asset management strategies.
Conclusion and Future Outlook
The intelligentization and automation of transformer oil filtration machines represent a significant leap forward in power transformer maintenance practices. By integrating advanced sensor technology, IIoT connectivity, sophisticated analytics, and automated control systems, these next-generation filtration solutions offer a compelling pathway towards enhanced efficiency, reduced costs, improved safety, and ultimately, a more reliable and resilient power grid.
Looking ahead, the field is poised for further advancements. We can anticipate the integration of even more sophisticated AI algorithms for more accurate predictive maintenance, the development of more compact and energy-efficient filtration units, and tighter integration with broader smart grid management systems. The continued embrace of intelligentization and automation in transformer oil management will undoubtedly play a pivotal role in ensuring the long-term health and performance of these critical assets that underpin our modern energy infrastructure.