Transformer Vacuum Pumping System: Ensuring Efficient Power Delivery
Power grids are the lifeblood of modern civilization, silently delivering electricity to homes, businesses, and critical infrastructure. At the heart of these grids lie transformers, vital equipment responsible for stepping up or down voltage levels to ensure efficient power transmission and distribution. However, a hidden enemy lurks within transformers – moisture and air. These elements can significantly compromise a transformer’s performance and lifespan. This is where transformer vacuum pumping systems come into play, acting as silent guardians that ensure the smooth flow of electricity by removing these detrimental elements.
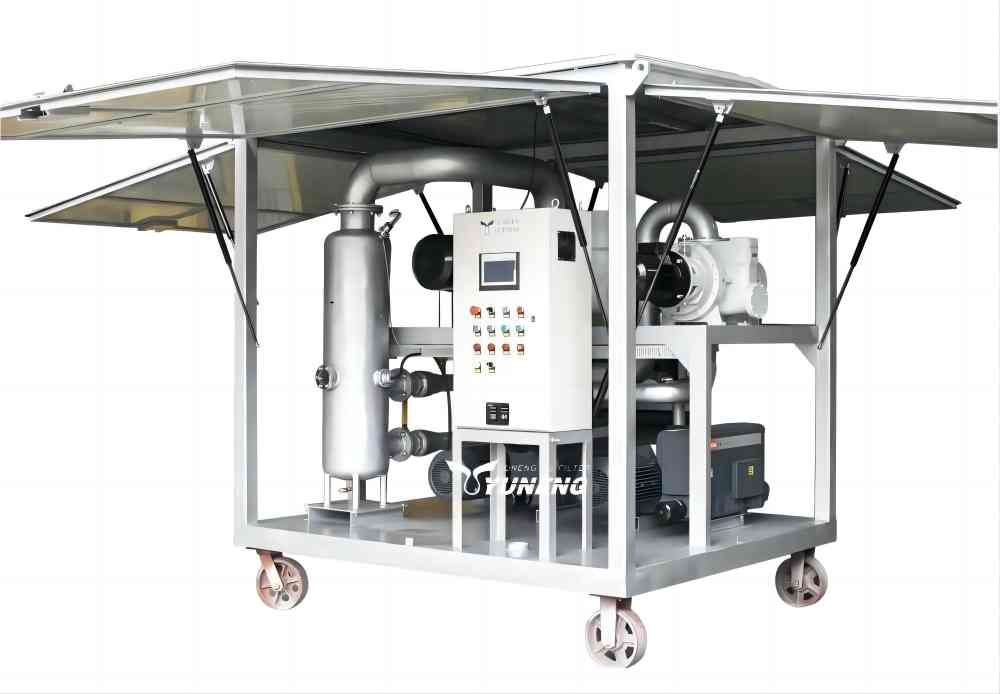
The Threats Posed by Moisture and Air in Transformers
Transformers rely on insulating materials, typically oil, to separate high-voltage internal components. When moisture or air is present within the transformer, it can create pockets of weakness in the insulation. This can lead to a phenomenon known as partial discharge, where small electrical arcs occur within the voids. Over time, these partial discharges can erode the insulation, leading to catastrophic electrical breakdowns. Additionally, moisture can cause internal corrosion and degrade the insulating oil itself.
The consequences of such breakdowns are severe. They can result in power outages, equipment damage, and even fires. As transformers are often located in critical substations or industrial settings, such disruptions can have significant economic and social repercussions.
How Transformer Vacuum Pumping Systems Safeguard Efficiency and Reliability?
Transformer vacuum pumping systems play a crucial role in mitigating these threats. Their primary function is to remove air and moisture from the transformer’s internal environment before it is filled with insulating oil. This drying process creates a vacuum within the transformer, significantly reducing the presence of air and moisture.
The benefits of transformer vacuum pumping are multifaceted:
- Enhanced Insulation Properties: By removing air and moisture, the system ensures that the insulating oil effectively separates the high-voltage components. This minimizes the risk of partial discharges and subsequent insulation breakdown.
- Improved Efficiency: Moisture reduces the transformer’s ability to conduct electricity efficiently. A properly dried transformer experiences lower energy losses, translating to cost savings and a reduced environmental footprint.
- Extended Lifespan: By eliminating the detrimental effects of moisture and air, transformer vacuum pumping systems contribute significantly to extending the operational life of these critical assets. This reduces maintenance costs and the need for premature transformer replacement.
Key Components of a Transformer Vacuum Pumping System
A transformer vacuum pumping system is a symphony of meticulously designed components, each playing a vital role in the drying process.
- Vacuum Pump: This is the workhorse of the system. Its primary function is to extract air and moisture from the transformer’s interior. There are two main types of pumps commonly used:
- Rotary Vane Pumps: These pumps utilize a rotating vane to trap and move air and moisture molecules. They are efficient for initial evacuation and excel at handling high volumes of gas.
- Roots Pumps: These pumps employ intermeshing lobes to achieve a higher vacuum than rotary vane pumps. They are typically used in the later stages of the drying process, where lower pressure levels are required.
- Condenser: This component acts as a moisture trap. As the pump extracts air and moisture from the transformer, the condenser cools the vapor, causing it to condense into a liquid state. This liquid is then collected and disposed of safely.
- Gauges: These instruments provide real-time monitoring of the pressure within the transformer. By observing the pressure readings, operators can assess the effectiveness of the drying process and determine when the desired vacuum level has been reached.
- Valves: These valves regulate the flow of air, moisture, and oil within the system. They allow operators to isolate specific sections of the system, control the pumping process, and facilitate oil filling after successful drying.
- Piping: A network of pipes connects all the components within the system, ensuring a smooth flow of air, moisture, and oil. These pipes are typically constructed from high-quality materials that can withstand the vacuum pressure and the properties of the transformer oil.
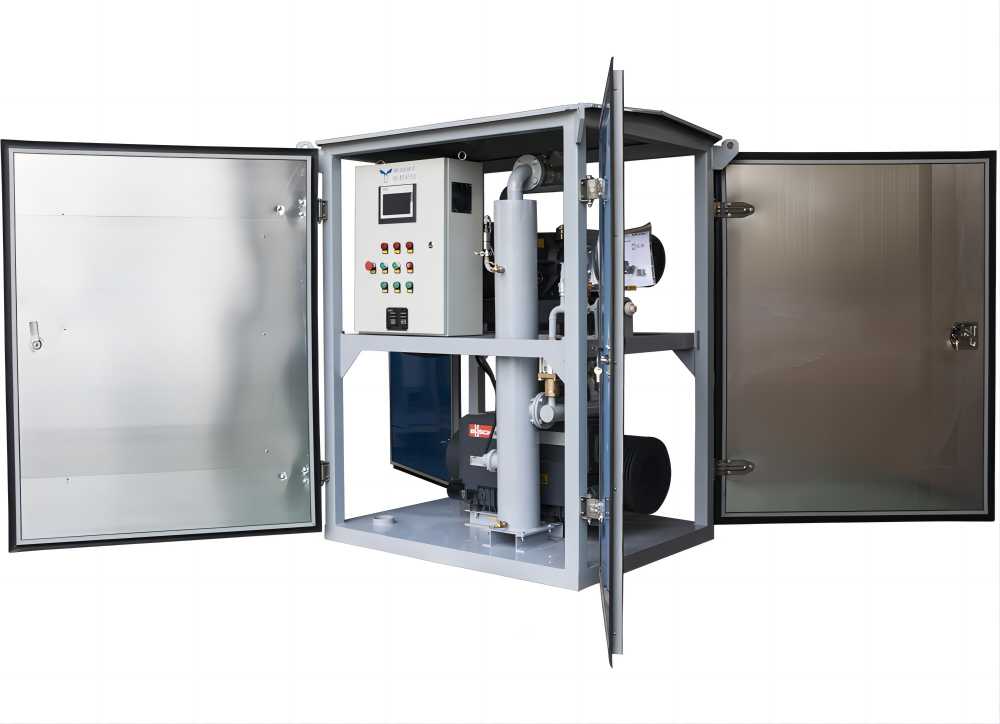
Guide to the Drying Process for Transformers
The process of drying a transformer through vacuum pumping involves several precise steps to ensure optimal performance:
- System Connection: The first step is to meticulously connect the vacuum pumping system to the transformer. This connection is crucial to establishing a proper seal, preventing any air leaks that could compromise the drying process.
- Activation of Vacuum Pump: Once the system is securely connected, the vacuum pump is activated. This initiates the crucial task of extracting both air and moisture from the interior of the transformer.
- Moisture Trapping: As the vacuum pump operates, it pulls air and moisture from the transformer. The vapor extracted is then cooled by a condenser, causing it to condense into liquid form. This liquid is efficiently collected within the condenser, effectively removing moisture from the system.
- Pressure Monitoring: Throughout the drying process, pressure gauges continuously monitor the pressure levels within the transformer. Operators closely observe these readings to determine when the desired vacuum level has been achieved, indicating successful moisture removal.
- Flow Control with Valves: Valves play a crucial role in the drying process by controlling the flow of air and oil. These valves are strategically adjusted to isolate specific sections of the system, optimizing pump efficiency and preventing contamination. Once the desired vacuum level is attained, the valves are carefully regulated to introduce degassed insulating oil into the transformer.
- Oil Filling: The degassed oil, devoid of air and moisture, is slowly introduced into the transformer through a dedicated filling line. Operators meticulously control the valves to ensure a steady and complete filling process, effectively displacing any remaining air pockets within the transformer.
- System Disconnection and Monitoring: Upon successful oil filling, the vacuum pumping system is disconnected from the transformer. However, the process does not conclude here. Continuous monitoring of the transformer’s oil is imperative to ensure its moisture content remains within acceptable limits. This monitoring typically involves periodic oil sampling and analysis using specialized equipment, ensuring the transformer’s optimal performance and longevity.
The Importance of Transformer Vacuum Pumping
The significance of the transformer vacuum pumping system cannot be overstated. They are the silent guardians that ensure the efficient and reliable operation of transformers, the backbone of the power grid. By removing air and moisture, this system:
- Minimize the risk of electrical breakdowns: This translates to fewer power outages, reduced equipment damage, and enhanced safety.
- Optimize transformer performance: A properly dried transformer experiences lower energy losses, leading to cost savings and a smaller environmental footprint.
- Extend transformer lifespan: By eliminating the detrimental effects of moisture and air, transformer vacuum pumping systems significantly contribute to extending the operational life of these expensive assets. This minimizes maintenance costs and the need for premature transformer replacement.
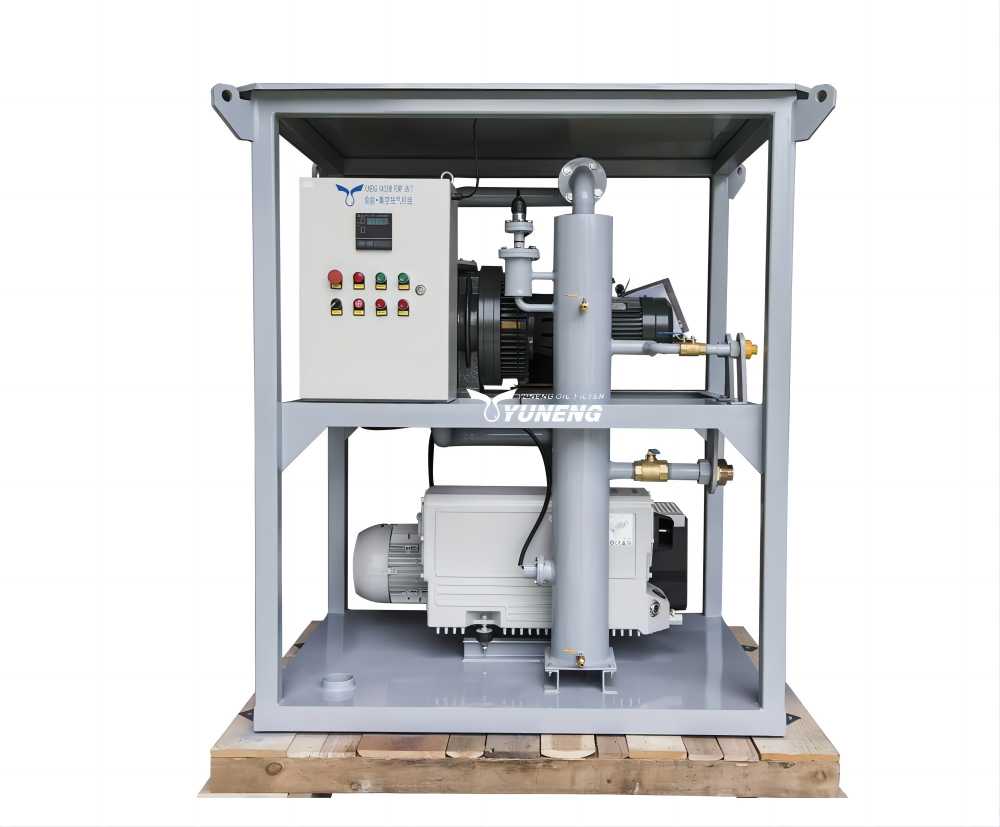
In conclusion, transformer vacuum pumping systems play a critical role in ensuring the smooth flow of electricity that powers our modern world. By safeguarding transformers from the detrimental effects of air and moisture, these systems contribute significantly to reliable power delivery, efficient energy usage, and ultimately, a more sustainable future.